Capacità ingegneristiche della gamma di sigillatura dei semiconduttori a Semicon Europa 2023
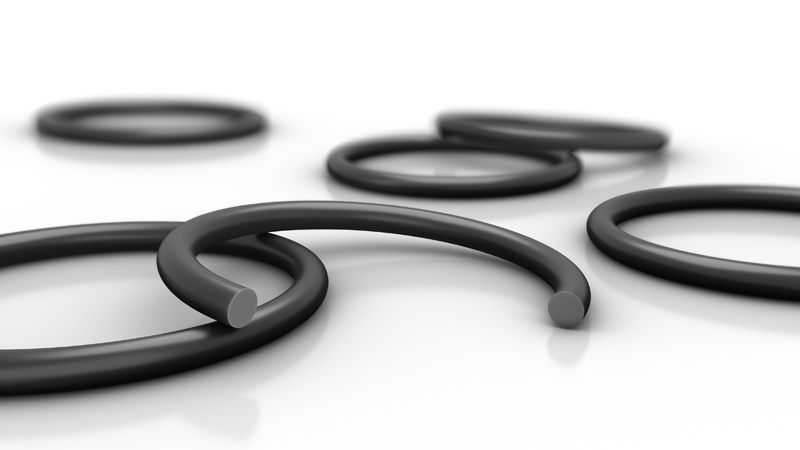
Chris Busby, Semiconductor Segment Manager, Trelleborg Sealing Solutions, says: “With the increasingly extreme temperatures and more aggressive chemical precursors used in semiconductor environments, reliable sealing solutions are essential to prevent premature failure. At Semicon Europa we will be featuring the latest additions to our semiconductor portfolio specifically engineered to address these challenges.
“Trelleborg offers customers premium engineering capabilities to develop the right custom solutions for today’s increasingly extreme fab and sub-fab environments, including the unique ability to model compression set data using finite element analysis. This step change in technology enables engineers to predict seals’ usable lifetime more accurately as they design and manufacture finished products.”
Isolast® PureFab™ - maximizing system uptime of advanced semiconductor processes
Trelleborg will showcase the latest additions to the extensive Isolast® PureFab™ range, including JPF40, an ultra-high temperature perfluoroelastomer (FFKM) developed for demanding subfab applications and thermal processes, including rapid thermal processing (RTP), atomic layer deposition (ALD) and oxidation. It offers unrivaled compression set performance at operating temperatures from +200 °C/+392 °F to +300 °C/+552 °F. This ensures sealing integrity for critical processes, withstanding peak application temperatures over +325 °C/+617 °F, the highest temperature capability of an elastomer material.
Isolast® PureFab™ JPF22 is an excellent all-round FFKM seal with superior chemical compatibility suitable for a wide range of semiconductor applications. The material offers excellent resistance to wet process chemicals and steam, as well as amine-based ALD precursors.
Isolast® PureFab™ JPF10 is a perfluoroelastomer with a fully organic formulation for use in the most critical semiconductor processes. It offers excellent vacuum integrity under aggressive process conditions and temperatures over +300 °C/+572 °F, as well as outstanding plasma resistance in a wide range of process gasses including NF3. Low particle generation and excellent outgassing performance means Isolast® PureFabTM JPF10 can increase process yields and lower the total cost of ownership of semiconductor processes.
>>Find out more about the Isolast® PureFab™ range
Innovative inflatable seals for access to plant, containers & rooms
Also showcased is the Airseal range of inflatable tubular elastomer seals activated by internal pressurization with air, water or other media, which excel in sealing access to plant, containers and rooms. Airseals represent a technically improved alternative to standard contact pressure seals and can be easily adapted to match the mating surface.
The Airseal range includes unique Thermal Processing Inflatable Seals made from high-grade EPDM and silicone rubber materials for load locks and access doors in advanced vertical thermal processors. The seals resist both vacuum and positive pressure, replacing traditional flat gaskets and O-rings, simplifying the hardware and speeding the overall processing operation.
The Airseal Load Lock Inflatable Seal/Clamp is a unique seal made of low-outgassing butyl rubber and is proven for vacuum service. It provides highly efficient and repeatable sealing in the patented vacuum load lock section of a fully automated electron beam metrology system used for sub-micron critical dimension measurement and integrated circuit imaging. With its unique blend of automation, measurement precision, and high throughput, the system meets and exceeds the process control needs of advanced semiconductor manufacturing. It simplifies the hardware necessary to achieve a seal in a vacuum and speeds the process of taking a wafer, loading it into the lock, and making critical measurements of its surface and its circuitry.
Sealing Solutions for the most demanding environments
The Isolast® K-Fab™ Flange Seal for critical subfab applications is temperature resistant for use up to +327 °C/+620 °F dependent on the material selection. It can be manufactured from a range of elastomer materials including Isolast® FFKM, Isolast® PureFab™ FFKM, PureFab™ Fluoroelastomer (FKM) for ultra-high purity, and standard FKM, and is suitable for combination with both aluminum and stainless steel.
>>Find out more about Isolast® K-Fab™ Flange Seal
In addition Trelleborg is showcasing the Turcon® Variseal® NW, part of the Variseal® range of spring-energized seals field-proven in extreme gas and liquid handling situations, including high vacuum and corrosive environments. The Turcon® case of flange seal encompasses an energizing spring that prevents possible contact between the spring or spring cavity and system media. It operates in extreme temperatures from -253 °C/-423 °F to +260 °C/+500 °F, is vacuum-capable in air to 10-9 mbar/l/s, and has excellent wear and friction characteristics. Compatible with virtually all media and gases including fluorine at high temperatures, it is available in custom sizes and standard dimensions with easy retrofit of current NW and KF elastomer seals.
>>Find out more about Turcon® Variseal® NW
Reducing friction with a nanoscale treatment
Also featured is Seal-Glide®, Trelleborg’s nanoscale surface treatment which improves on the friction and sticking performance of conventional coatings. Applied through an innovative process, it leads to a finish up to 50 times thinner than many conventional coatings. The technique also enables treatment of components with complex geometries and features, such as undercuts, that would otherwise be impossible with lacquer-based coatings. Even after being stretched, Seal-Glide® returns to a smooth finish with no breakouts, maintaining its improved sliding properties. Seal-Glide® increases the lifetime of the complete sealing system, boosts assembly and operation of products, has very low outgassing and particle generation, and improves performance through significant reduction of friction and stickiness.
>>Find out more about Seal-Glide®
A step change in modeling seal longevity
Trelleborg will also demonstrate its extensive and rigorous engineering capabilities, including the unique ability to model the compression set of elastomers to predict seal lifetime using finite element analysis (FEA) for its semiconductor customers. This approach enables engineers to capture more accurate seal compression set data compared to industry standard simulation compression set tests, allowing for more accurate predictions about seal longevity. Our extensive ability to work with customers to develop custom seals for specific applications will also be highlighted.
>>Find out more about modeling compression set data to predict seal lifetime using FEA
>>Find out more on Trelleborg’s wide range of solutions for semiconductor applications