Sealing Solutions for Injection Molding Machines
Hydraulic cylinders and other equipment on injection molding machines require complex sealing solutions to support challenging operating conditions. These cylinders are expected to operate continuously for long periods of time without any loss of efficiency.
Explore injection molding machine applications by clicking on the different application areas.
Contact us for support with your injection molding machine application
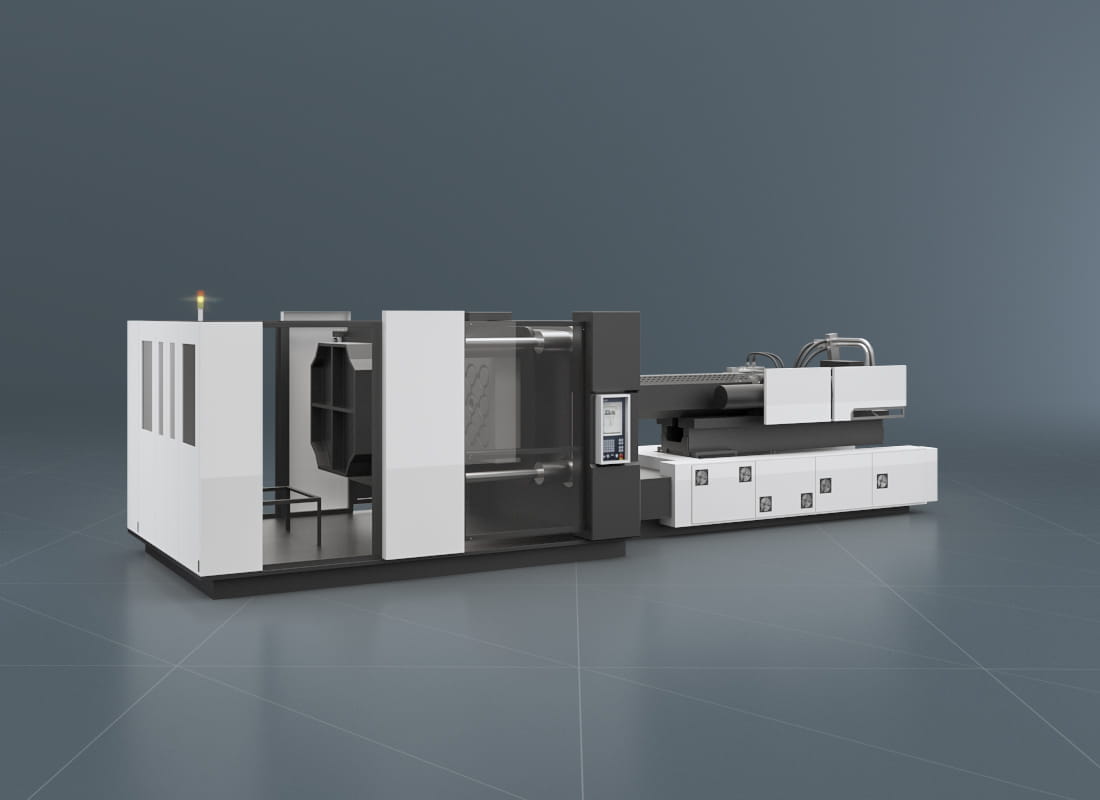
The injection cylinder drives the linear movement of the injection screw and must deliver consistent force to inject the proper amount of material into the mold during each cycle.
Employing revolutionary Lubrication Management technology, seals act together in complex configurations to optimize friction and wear to radically increase application lifetime and reliability, while scrapers exclude external media that could damage the sensitive hydraulic system.
Recommended sealing solutions: Orkot® Slydring, Turcon® Glyd Ring® T, Turcon® Stepseal® V LM, Turcon® Stepseal® 2K, Turcon® Excluder 5
Product highlight: In this configuration Turcon® StepSeal® V LM acts as a primary rod seal with outstanding tribological performance. Utilizing a patented hydro-static pressure release channel, it helps avoid over-pressure and consequential damage.
The clamp cylinder maintains pressure on the mold to ensure parts are formed correctly. Depending on the speed of the molding process, this cylinder must work continuously in a short stroke environment. Special low friction seals can provide long life in these conditions.
Recommended sealing solutions:
Slydring® in HiMod® or Orkot® Zurcon® U-Cup RU9, Zurcon® Scraper DA 24, Turcon Glyd Ring® T, Turcon Glyd Ring® Hz, Turcon® Excluder 5
Completed parts can be ejected from a mold in several ways: air, spring-actuation, hydraulic actuation, or even by a robotic arm. For hydraulic actuation, the ejector cylinder moves a plate with mechanical components that are specifically designed to push parts out of the mold. As this cylinder must operate on every injection cycle, low friction and long life are required to ensure the fine movements are repeatable and that they fully remove parts each time.
Recommended sealing solutions:
Turcon® and Zurcon® seals, Orkot® and HiMod® bearings
The mold stroke cylinder brings the platens into position prior to the molding process, thus allowing the clamping cylinder to provide the extension and retraction force for each cycle. These cylinders may only actuate a few times a day, making low stick-slip seals an important requirement.
Recommended sealing solutions:
Orkot® Slydring, Turcon® Glyd Ring® T, Turcon® Stepseal® 2K and Turcon® Excluder 2
The rotating injection unit in an injection molding machine drives the molding material through the injection screw, where the combination of movement and heat melts the material prior to it being injected into the mold. This operation is continuous during the molding process; therefore, seals must be robust and have low friction characteristics.
Recommended sealing solutions:
Turcon® Roto VL® Seal F, Turcon® Buffer Ring, Radial Oil Seal
Injection Cylinder
The injection cylinder drives the linear movement of the injection screw and must deliver consistent force to inject the proper amount of material into the mold during each cycle.
Employing revolutionary Lubrication Management technology, seals act together in complex configurations to optimize friction and wear to radically increase application lifetime and reliability, while scrapers exclude external media that could damage the sensitive hydraulic system.
Recommended sealing solutions:
Orkot® Slydring, Turcon® Glyd Ring® T, Turcon® Stepseal® V LM, Turcon® Stepseal 2K, Turcon® Excluder 5
Product highlight:
In this configuration Turcon® Stepseal® V LM acts as a primary rod seal with outstanding tribological performance. Utilizing a patented hydro-static pressure release channel, it helps avoid over-pressure and consequential damage.
Clamp Cylinder
The clamp cylinder maintains pressure on the mold to ensure parts are formed correctly. Depending on the speed of the molding process, this cylinder must work continuously in a short stroke environment. Special low friction seals can provide long life in these conditions.
Recommended sealing solutions:
Slydring® in HiMod® or Orkot®, Zurcon® U-Cup RU9, Zurcon® Scraper DA 24, Turcon Glyd Ring® T, Turcon Glyd Ring® Hz, Turcon® Excluder 5
Ejector Cylinder
Completed parts can be ejected from a mold in several ways: air, spring-actuation, hydraulic actuation, or even by a robotic arm. For hydraulic actuation, the ejector cylinder moves a plate with mechanical components that are specifically designed to push parts out of the mold. As this cylinder must operate on every injection cycle, low friction and long life are required to ensure the fine movements are repeatable and that they fully remove parts each time.
Recommended sealing solutions:
Turcon® and Zurcon® seals, Orkot® and HiMod® bearings
Mold Stroke Cylinder
The mold stroke cylinder brings the platens into position prior to the molding process, thus allowing the clamping cylinder to provide the extension and retraction force for each cycle. These cylinders may only actuate a few times a day, making low stick-slip seals an important requirement.
Recommended sealing solutions:
Orkot® Slydring, Turcon® Glyd Ring® T, Turcon® Stepseal 2K, and Turcon® Excluder 2
Rotating Injection Unit
The rotating injection unit in an injection molding machine drives the molding material through the injection screw, where the combination of movement and heat melts the material prior to it being injected into the mold. This operation is continuous during the molding process; therefore, seals must be robust and have low friction characteristics.
Recommended sealing solutions:
Turcon® Roto VL® Seal F, Turcon® Buffer Ring, Radial Oil Seal