Taking A Look At Thermoplastic Driveshafts - Trelleborg
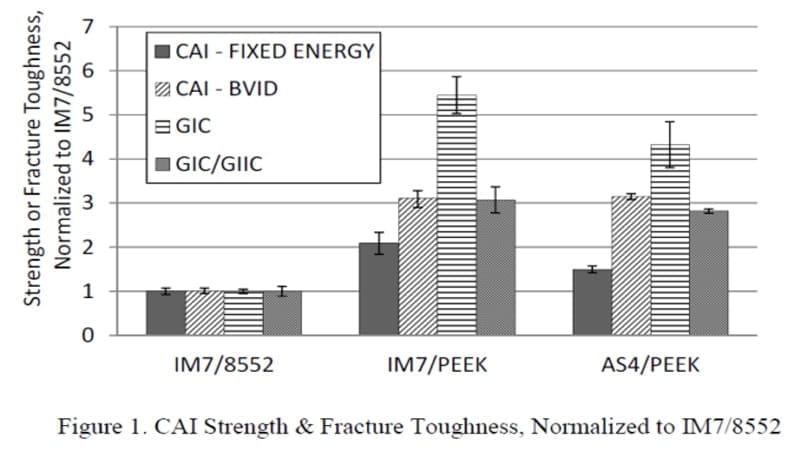
Driveshafts exist in a wide variety of applications spanning aerospace, automotive, and industrial markets. Just as varied are the materials used to manufacture these driveshafts. At Automated Dynamics, we emphasize the value and benefits of Thermoplastic Composites.
Using Automated Fiber Placement allows for strong, highly customized, lightweight parts built to maximize performance. Depending on need, a designer can specify key characteristics such as thickness and fiber angle, resulting in the ideal part for your project. Examples include adding axial plies to improve bending stiffness or additional 22⁰ plies to improve max torque after damage.
Innovative Engineering
But the benefits don’t begin and end with customization. The engineering properties of thermoplastics are impressive, and they directly improve performance. Below, we break down some of these impressive features and reveal how they aid in creating higher performing driveshafts.
- Thermoplastic Driveshafts can be consolidated as they are being processed which eliminates costs of post processes such as an oven or autoclave cycle.
- Thermoplastics are known for their chemical and environmental resistance. This includes excellent resistance to strong acids, organic solvents, alcohols, fuels, UV radiation, and many others.
- These driveshafts can be used in any application that requires exceptional tailored performance.
- Recently, advanced NDI techniques have been able to detect defects on any ply within the part. This further improves the quality and robustness of our parts and manufacturing process.
- The dynamic properties of a driveshaft can be controlled by layup design to increase the critical speed, maximizing RPM.
- No de-bulking is required allowing for very thick cross sections without the fear of fiber marcelling.
Superior Materials
While any thermoplastic can offer these benefits, IM7/PEEK offers the best combination of material properties. Specific properties include:
- IM7/PEEK has a specific energy absorption of 180 kJ/kg which is among the highest values recorded for any material (~800% greater than aluminum).
- Its ability to be fiber placed gives designers the flexibility they need to design the optimal layup for a given application.
- IM7/PEEK tape is thinner than IM7/8552 tape (0.0045” vs 0.0072”) which allows for more plies for a part with equivalent thickness. For example, 18 plies of 8552 tape has the equivalent thickness and weight of 28 plies of PEEK tape. This allows for more “resolution” in the layup design.
- It has a ~35% greater undamaged torque and a ~280% greater damaged torque than an equivalent thickness IM7/8552 shaft. This data we acquired as part of a NAVAIR SBIR for a light weight, highly survivable drive shaft.
- It has a mode 1 fracture toughness that is ~5 times greater than that of IM7/8552 and a mode 2 fracture toughness that is ~3 times greater.
Reference: Levine, S., Dequine, D., Lamm, B.. “Damage Tolerance of Thermoplastic Stretch-Broken Carbon Fiber vs. Continuous Carbon Fiber Pre-Preg” SAMPE International Conference & Exhibition, Long Beach, CA, May 2013
(GIC represents mode 1 fracture toughness, GIIC represents mode 2 fracture toughness, CAI is compression after impact)
For more information about our driveshaft programs, contact:
Gabriel Benarroch
Business Development Manager
518.377.6471 ext.212| Email Gabriel