Trelleborg Supports Sustainability with Thermoplastic Composite Solutions at JEC World
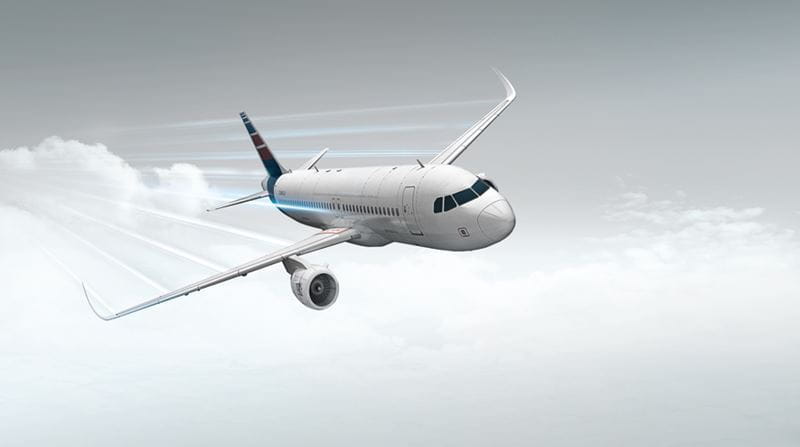
Specialist Thermoplastic Solutions
Attendees can learn about specialist continuous-fiber thermoplastic composite manufacturing process, which uses Automated Fiber Placement (AFP) technology to place pre-impregnated unidirectional composite tapes needed to produce strong, light-weight components. The manufacturing process utilizes In-Situ Consolidated (ISC) technology that requires no autoclave or other post processes to eliminate fibre wrinkling and offer an unlimited choice of fibre angles.
Reid Hislop, Product Manager at Trelleborg Sealing Solutions, says: “Thermoplastic composites offer extreme toughness while being able to create the lightest weight parts, making them ideal for aerospace applications where reducing weight is vital. Lighter components use less fuel and support the move to green transportation. Unlike traditional thermoset composites, thermoplastic composites can be recycled at the end-of-life.
“Thermoplastics are lighter in weight with high damage tolerance, outstanding fatigue life, dampening properties, and are solvent and chemical resistant. This makes them ideal for a wide range of aerospace applications. JEC World is a fantastic opportunity for us to meet with key decision makers and industry specialists to discuss custom solutions for complex applications.”
In-situ Consolidation Technology
In-Situ Consolidation thermoplastic composite technology utilizes a melt-bond process for rapid forming of components without adhesives, fasteners or welding. This unique process gives you the ability to bond to differing materials which can result in the creation of new, hybrid structures.
On display is a thermoplastic drive shaft that is up to 90 percent lighter than a titanium alternative; a stiffened carbon fiber panel created using the specialist continuous-fiber thermoplastic composite manufacturing process; and a two-part, cobonded multi-material bearing for landing gear and actuator applications, manufactured using a melt-bond process to combine a low friction Polyetheretherketone (PEEK) or Polytetrafluoroethylene (PTFE) liner, and a Carbon Fiber reinforced PEEK outer composite for strength and durability. Technical experts will be on hand to discuss custom applications and requirements.
Learn More
>> Find out more about advanced composites for aerospace
>>Download the press release
>>Download the press image
>>Get in touch to discuss your project