Cheers to sustainability
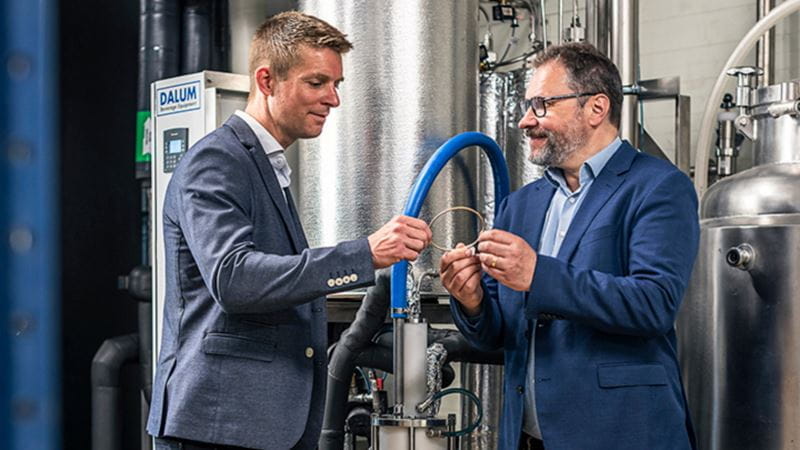
Craft breweries are relatively small, independently owned, employ traditional brewing methods, and emphasize flavor and quality. Alongside making great beer, it’s about much more: creativity, innovation, passion and stepping outside the box. Brewers are fun to work with, motivated and passionate about what they do.
The craft brewing industry also has a lot of potential. The sector is continuously growing, both in value and in volume, globally at over 14% annually. Alongside offering exciting new flavors and tastes, breweries are expanding their distribution networks locally and internationally. Consumers are increasingly preferring craft over mainstream beers because they offer new styles and flavors, and use premium quality ingredients, which are often locally sourced.
“The craft segment is where all the growth is; it’s exciting and so much is happening there. That is the main reason why I decided to focus on craft beer when I started my company. I'm now trying to help craft brewers save money and become more environmentally friendly by reducing emissions,” says Kim Dalum, the founder and CEO of Dalum Beverage Equipment.
Upon founding his company, Dalum approached several craft breweries with different ideas for new equipment and collaboration, based on his previous experience with large commercial breweries. The craft breweries showed interest in the creation of an affordable, small system to capture and compress CO2.
In 2019, Dalum started a partnership with Ørbæk Brewery to develop a piece of equipment, which would capture CO2 emitted during the fermentation process and compress it for storage and reuse at a later stage.
“We quickly realized there was no existing technology available, so we would have to completely build everything ourselves,” says Dalum. “This was a true development project with a lot of turbulence and changes based on trial and error.
“We knew we would need a seal supplier to help develop a sealing solution for the compressor unit and reached out to a number of companies. We were looking, not only for someone to supply sealing components, but also one with expert knowhow and a partner who could help us evaluate and specify seal designs and materials for our equipment. Trelleborg expressed a lot of interest in collaborating with us.”
Collaboration with the local Trelleborg solution center in Denmark and the Helsingør manufacturing site was easy. The Trelleborg team provided guidance throughout the entire process, analyzing the seals after testing to understand how they were functioning in the equipment and what adjustments needed to be made, both to the seal and to the hardware.
Dalum recalls: “One story from early on in our partnership highlights the important role Trelleborg played. Analysis on a Zurcon® engineered plastic seal, a standard material for applications such as ours, showed that CO2 was forming carbonic acid somewhere inside the compressor. This caused the stainless steel in the equipment to rust and build a black slurry, which was damaging the seals. The discovery led us to add additional filters to the system to make the equipment run cleaner.”
In March 2020, after just over one year, Dalum’s first CO2 Recovery Plant was up and running at the Ørbæk Brewery. This was a big milestone.
“While I was familiar with similar systems in large breweries, it was very challenging on such a small scale,” continues Dalum. “Many things had to be rethought and redesigned along the way and we were limited with price constraints, which is precisely why something like this had not been possible before in medium and small breweries.”
After installation of the first system, Dalum was ready to sell the equipment. October 2020, saw the installation of a second CO2 Recovery Plant at the Svaneke Brewery on the Danish Island of Bornholm. After implementation of the CO2 Recovery Plants at two breweries, Dalum sees two next steps for Dalum Beverage Equipment.
“First, we want to create a version of the Recovery Plant, designed for smaller microbreweries. And, at the same time, we want to scale up production of the existing Recovery Plant, so we can make it available to a larger number of breweries in a smaller span of time. With this, we need to shift to design for manufacturing and serial production,” says Dalum.
To find out more please visit:
Press Service:
If you reproduce information from this release please give contact details as:
www.trelleborg.com
E-mail: news@trelleborg.com