Save the Mushrooms
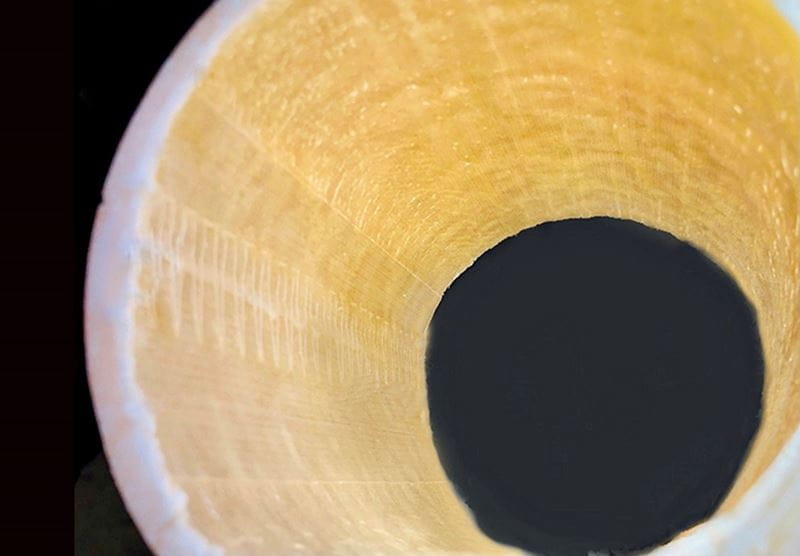
Cured in place pipe lining has come a long way since the year 1970, when—as the story goes— an Englishman by the name of Eric Wood developed the first cured-in-place piping. He was an agricultural engineer hired by a mushroom farm to find a solution for the repair of an air duct without disturbing the fragile beds of mushrooms below it. Woods lined the duct with felt fabric that had been soaked in resin. Once it hardened, the pipe was repaired, and the mushrooms continued flourishing beneath it. Just a year later, the same technique was used to rehabilitate an egg-shaped sewer on the East End of London.
This “no-dig” method is now common across the world due to its non-invasive process. Research and technology continue to evolve. That’s where Trelleborg enters the game.
Pipecure Flex™: An eco-friendly solution
In 2021, Trelleborg officially launched Pipecure Flex™, a PVC-free, environmentally responsible cured-in-place liner fabric that can be impregnated with thermosetting resins and retrofitted into old pipes and then cured in place.
It is projected that $2.5 billion will be spent on the rehabilitation of sewer pipes in 2022, and a staggering $1 trillion within the next 20 years. With numbers like these, Trelleborg saw a need to develop a CIPP product that is not only effective but sustainable.
Pipecure Flex™ is manufactured with a solvent-free process that uses less energy and space. This reduction of pollutant emissions reduces the negative impact not only on humans and the surrounding production environment but also air quality, plant and animal life.
“We are doing our part to be an environmentally responsible company from our polymer selections to our manufacturing processes,” says Adelyn Hill, Product Manager of Trelleborg Pipecure Flex™. ”Our bespoke 100% solids polyurethane formulation eliminates the release of hazardous VOCs into the atmosphere.”
”Our manufacturing process does not require the use of a thermal oxidizer which further reduces energy consumption. This is the first stop for Pipecure Flex™ on its sustainable sustainable journey. We are constantly researching new and exciting solutions,” says Hill.
Flexibility for any possibility
Pipecure Flex™ is an extremely versatile liner fabric, as it is compatible with most resin systems (epoxy, polyester, polyester styrene, vinyl ester), installation methods (inversion and pull in place), and curing methods (ambient, hot water, and steam).
It is suitable for use on lateral and vertical pipes and accommodates bends up to 90 degrees with minimal wrinkling. Additionally, it is capable of transitioning between widths and has a low coefficient of friction.
“Trelleborg has a long track record of focusing our product development efforts on the challenges affecting our customers most,” says Antony Croston, Director of Product Development at Trelleborg Engineered Coated Fabrics. “Minimal environmental impact and maximum value are key benefits that our customers continually request to differentiate their own offerings against competing solutions. We will continue to improve these market-leading products to be more sustainable and functional.”
The future of Pipecure Flex™ is continued growth and innovation with sustainability leading the way. A target launch is planned for early 2022 for a version made with up to 100% recycled plastic fibers.
To learn more about Pipecure Flex™, visit Pipecure.com, or email us directly at ECF@Trelleborg.com.