Trelleborg Showcases its Global Medical Molding Competence at Compamed
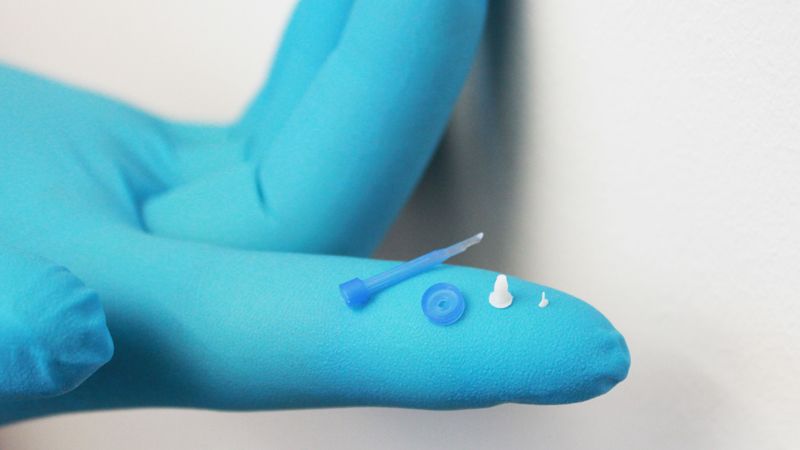
At Compamed, Trelleborg’s healthcare & medical operation will highlight its global engineering expertise by showcasing its medical molding capabilities.
As a world leader in precision Liquid Silicone Rubber (LSR) and Two-Component (2C) molding processes, Trelleborg supports its customers in the creation of complex geometries, including multi-component parts, and continually focuses on eliminating the need for secondary component assembly. This removes the cost and risk associated with assemblies, such as potential leak paths or undesirable spaces for bacterial growth. It also provides the developer with much greater design latitude to create considerably more robust and cost-effective solutions.
Ursula Nollenberger, Product Line Director, Healthcare & Medical, says: “We have over the past few years made significant investments in high-precision medical molding. It is part of Trelleborg’s strategy to strengthen its positions in selected attractive market segments.
“Silicone is considered the gold standard of materials in the healthcare and medical segment due to its biocompatibility, inertness, and favorable physical and haptic attributes. Trelleborg is a world leader in high precision LSR and multi-component LSR processing. Multifaceted geometries are produced at our strategically positioned global manufacturing facilities in a consistent way, with the same processes worldwide.”
One of Trelleborg's most outstanding capabilities is 2C LSR Technology, the simultaneous injection of LSR in combination with engineered plastics. In what is also commonly referred to as 2K, 2shot, multi-component injection molding, or co-injection, Trelleborg employs highly advanced and sophisticated tool and process engineering to develop innovative solutions, combining two or more individual materials into one fully bonded, robust component in hard-soft and soft-soft combinations.
Alternatively and depending on part geometry and material combinations, parts can be overmolded to provide fully-bonded custom solutions produced in two steps, combining silicone with mostly plastic or metallic substrates in a variety of hard-soft combinations.
Also on display will be micro and nano technology, where components can be produced below 10 milligrams in weight. These are ideally suited to medical devices, which are continually being reduced in size. The manufacture of these tiny parts is achieved through flashless production that is made possible with proprietary needlepoint injection technology, fully automated parts handling and special tool construction. Thin membranes component sections can be as thin as 0.10 mm / 0.004 inch or less with no pin holes, and perfect consistency in thickness and quality.
Trelleborg experts will be on stand F02 in hall 8a at Compamed in Düsseldorf, Germany, November 18 to 21 to discuss medical molding. For further information on medical molding go to https://www.tss.trelleborg.com/en/healthcare/products-capabilities/custom-shapes.