Trelleborg Demonstrates how Lubrication Management and Counter Surfaces Technology Can Make Hydraulic Applications More Sustainable
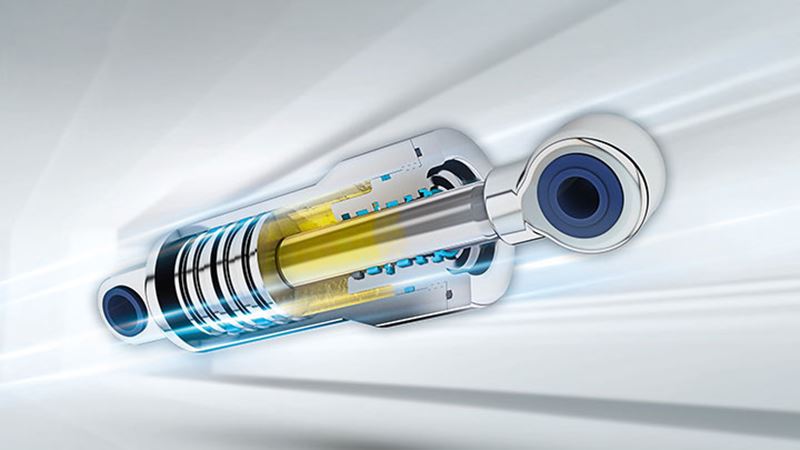
Lubrication Management not only extends seal life, but it also significantly reduces friction, lowering the energy required to power hydraulic systems and potentially allowing for the downsizing of drive components. Closely linked to Lubrication Management, Trelleborg’s surface coating research enables optimization of alternative surfaces to chrome, which is now banned as a counter surface due to environmental regulations.
Dr. Mandy Wilke, Senior Manager Global Technical and Intellectual Property Management at Trelleborg Sealing Solutions, says: “Lubrication Management is more than choosing and applying a lubricant. It’s about managing and adjusting the lubrication conditions of all elements within a sealing system, reducing the load on each element and optimizing the friction-wear lifetime of the system.
“A more holistic approach to machine maintenance, Lubrication Management focuses on friction points: the seals and bearings and the interfaces between surfaces in motion that are constantly subjected to pressure and wear. When friction is minimized, the risk of system damage and failure is often lowered. Additionally, the resulting increase in energy efficiency can allow for lower energy density within the system, thus reducing potentially harmful heat sources.
“With an aim to reduce unplanned downtime and cost, while upholding the integrity of the sealing system, fluid power experts must assess the problem before devising the right solution through materials, application, and maintenance.
“Traditionally, piston rods in hydraulic systems were chrome plated to provide corrosion resistance as well as friction and surface finish characteristics; however, this it no longer a sustainable option. Under the REACH directive, Hexavalent Chromium (CR6) must now be omitted from any hydraulic application, leading to the adoption of alternative coatings for the hydraulic cylinder´s piston rods. To maximize the performance and seal life expectation in hydraulic actuators, these should be designed to optimize a system’s tribology, which is dependent on the interaction of seals, hydraulic fluid, and the finish of the mating surfaces.
“The lubrication within the hydraulic system fundamentally affects the surface finish of the mating surfaces. Their characteristics will determine the lubrication within the system and, therefore, the tribological environment and ultimately the overall energy usage of the system.”
Trelleborg Sealing Solutions provides resources relating to Lubrication Management and counter surface technology. These include webinars, brochures, and whitepapers. Go to: Fluid power
Press Service:
This press release is available for download in English. If you reproduce information from this release please give contact details as:
www.trelleborg.com
E-mail: news@trelleborg.com