High hopes
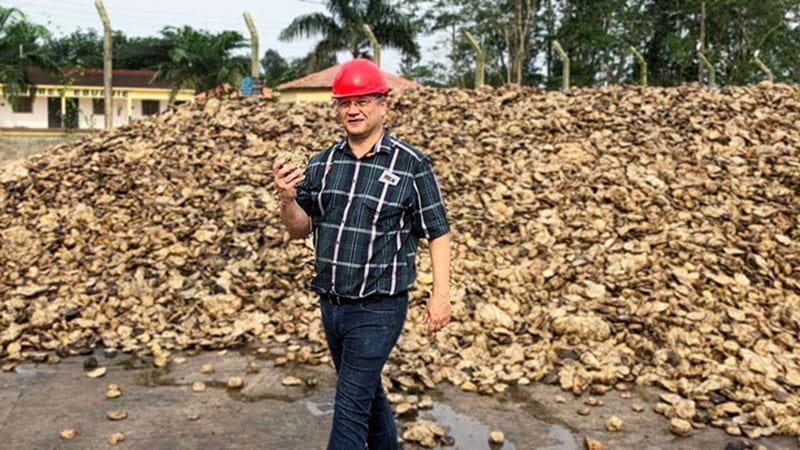
Synthetic rubber dominates the market – and yet almost half the rubber used by the manufacturing industry is natural. While Thailand and Indonesia are the two biggest producers of natural rubber, the third country on the list in terms of net exports is the Ivory Coast.
One of the producers there is SAPH, an important supplier of natural rubber to Trelleborg and its natural rubber producer in Bongo, in the southeast of the Ivory Coast, is the largest in Africa. It can produce 56,000 tonnes of natural rubber per year.
Rubber can be harvested every month of the year except January and February. Siphoned off from the Hevea Brasiliensis tree, the raw materials are collected in a cup, where they coagulate to form what is known in the industry as a “cup lump”. The color of the cup lump changes depending on how much time it spends drying out in the sun, becoming more yellowish-brown with increased exposure and oxidation.
SAPH Quality Manager Etienne Bertrand says: “The first step we take with a batch is quality control – to check that the raw material contains enough usable rubber.
After that comes the washing, mixing, cutting and drying process.”
Among the most striking features of the facility are the prominent graffiti-like reminders on the walls to wear safety equipment including helmets, boots, visors and, if necessary, ear protection. The reminders are clearly being taken seriously; the accident rate has decreased in the past few years, with only 13 recorded in 2017, which is comparable to any similar industrial production facility in Europe.
The initial washing phase involves the use of a great deal of water in large tubs. The facility has recently invested in a comprehensive water cleaning site, where the aim is to recycle the water.
The recycling process has not yet been perfected, but it has reached a level where the purified water can be used for the first step of the industrial process for things like watering plants.
Having been dried, a finished bale of yellow-brown natural rubber weighs 35 kg. Wrapped in plastic sacks, 36 bales are then stacked on a pallet.
Around 2,000 tonnes of natural rubber of varying degrees of quality are stored on pallets in the large warehouse at the end of the production chain. Every pallet is inspected at the internal laboratory where obligatory tests are carried out to ensure quality and detect any impurities. The test results are saved so that batches can be tracked and cross-checked.
On the plantation, the high-tempo tapping work is in full swing. A tapper has less than 20 seconds per tree to make the right cut and empty the cup to collect the rubber. Everyone has gone on a 21-day course to learn how to make the optimal cut.
Supporting its workforce is vital to SAPH. Employees enjoy many benefits such as the opportunity to live in the nearby villages that the company has built which are directly connected to the factory. They also have free access to water and electricity in their living quarters, daycare facilities and places at locally run primary schools for their smaller children, and — not least — basic insurance and health care.
The significant fixed costs involved in taking proper care of the workforce fall under the heading Corporate Social Responsibility (CSR). It is perhaps mainly this aspect of comprehensive social responsibility that differentiates a manufacturing facility of this size in this part of Africa from any in Western Europe or North America.
Henriette Gomis-Billon, who is responsible for sustainability and communication for the SIFCA Group, the main owner of SAPH, says: “There really is no alternative.We have to take on a great deal of responsibility, otherwise it would be impossible to run an operationas large as ours, with almost 1,300 employees.”
Another positive result of SAPH’s CSR efforts is that the villages neighboring the ones owned by the company also benefit. They can also use the health center and receive advice and help from doctors and nurses, for example during childbirth. In general, the quality of equipment here is higher than at the equivalent state-owned health facilities.
Many other services that the state would usually provide are taken care of by the large rubber producer in this region – and access is not limited to those living in the company’s villages.
In the areas just outside these villages, SAPH provides support to high schools in the form of materials and the construction of new buildings. The company also builds school canteens with support from local women’s groups for food supply and preparation, using the motto “a hungry belly has no ears”.
An entire ecosystem has sprung up around the facility in Bongo. And the operation has given independent rubber farmers a chance to earn an income that is better than if they were growing cacao, which you can only harvest twice a year.
For more information, please go to:
https://www.trelleborg.com/en/sustainability/resources
This is an article has been reproduced from Trelleborg's T-Time magazine. To download the latest edition, go to: www.trelleborg.com/t-time
Press Service: This article is available in eight languages. Media are welcome to use this article in their own publications. To download the article and pictures in any language go to https://bamboo-contentpartner.com/. If you reproduce information from this release, please give contact details as: www.trelleborg.com.