Skol to a Sustainable Beer
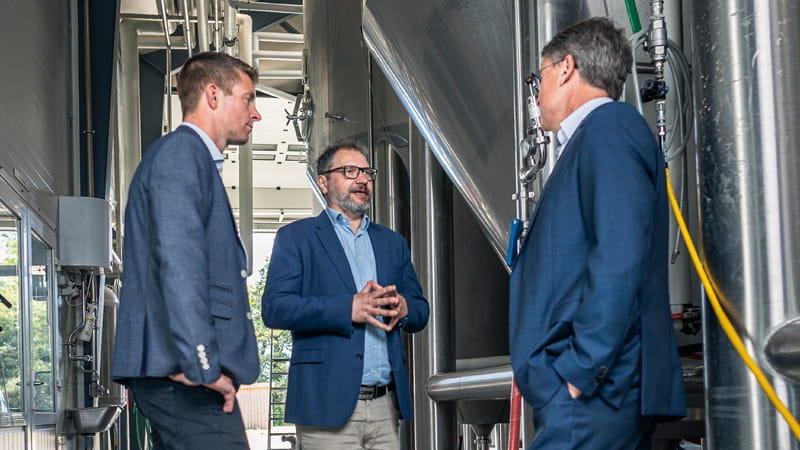
IN SHORT
- Trelleborg Sealing Solutions collaborated with Dalum Beverage Equipment in the development of a CO2 compressor.
- The compressor is one part of a CO2 recovery plant, enabling craft breweries to recycle CO2 emitted during fermentation.
- Turcon® MF6 is the optimum material in the compressor's challenging operating environment
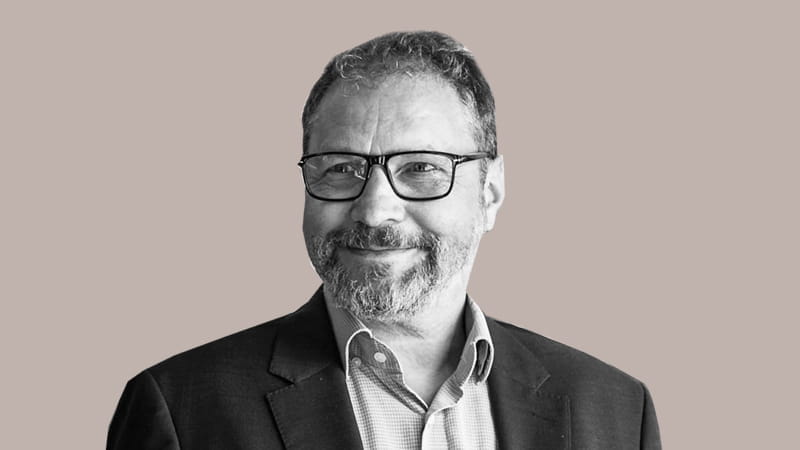
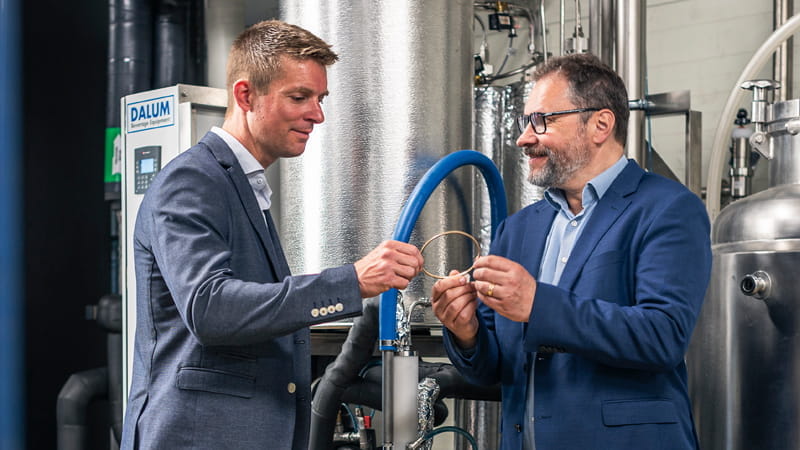
“The craft segment is where all the growth is; it's exciting and so much is happening there. That is the main reason why I decided to focus on craft beer when I started my company. I'm now trying to help craft brewers save money and become more environmentally friendly by reducing emissions,” says Kim Dalum, the founder and CEO of Dalum Beverage Equipment.
As we look to the future, identifying and developing ways to be more sustainable is becoming increasingly important. The craft brewing industry is fully invested in this, whether by using organic, local ingredients, or making the brewing process more environmentally friendly.
“This is where I was determined to help make an impact,” Kim explains. “After spending much of my professional life developing equipment for larger breweries, I founded Dalum Beverage Equipment to give craft and microbreweries the same innovations, enabling them to be more sustainable. We work closely with the brewers, bringing our engineering expertise and knowhow to co-develop equipment that will make a difference in the brewing process.”
The CO2 produced at this stage is emitted from the beer. The ability to capture and recycle this gas has numerous benefits:
- Improves the workplace environment - high concentrations of CO2 can displace oxygen, resulting in so-called “CO2 headaches,” drowsiness and general discomfort. Capturing this gas significantly improves the well-being of brewery staff.
- Reduces carbon footprint - CO2 is the primary greenhouse gas emitted through human activity. Larger emissions of greenhouse gases can lead to very high concentrations in the atmosphere, which can trap additional heat, contributing to global warming.
- Financial savings - craft breweries have had to buy CO2 to use, either later in the brewing process (bottling) or in the production of other beverages (e.g. soft drinks). By capturing and recycling the CO2, the gas naturally produced during fermentation can be used again.
- Guarantees supply – brewers control the source of CO2, facilitating organic production and brewing according to the German purity law.
Large, commercial breweries have the technology and resources to recycle CO2, but small breweries have not been able to capture the gas. Instead, it is typically discharged into the production room, while at the same time, CO2 is purchased in tanks for later use in the filling and bottling process.
Equipment to support recycling of CO2 produced during the brewing process could potentially have a huge impact on the craft brewing market. The biggest challenge would be developing a solution on a smaller scale, that brought all the benefits, while remaining cost effective.
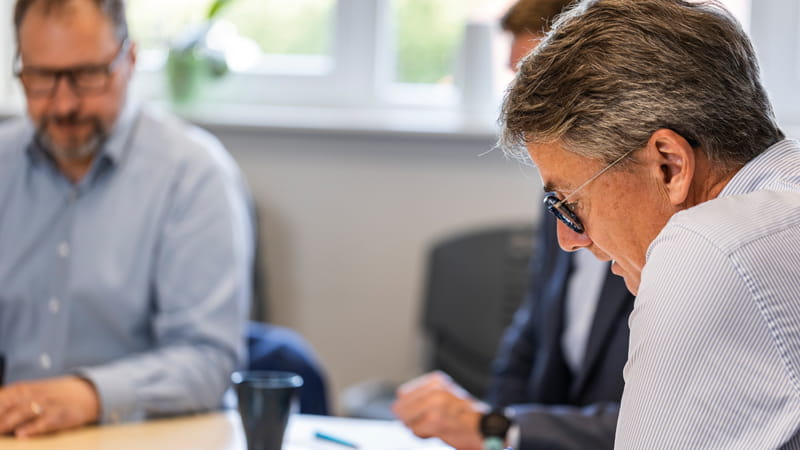
Collaboration with the local Trelleborg Customer Solution Center in Denmark and the Helsingoer manufacturing site was easy. The Trelleborg team provided guidance throughout the entire process, analyzing the seals after testing to understand how they were functioning in the equipment and what adjustments needed to be made, both to the seal and to the hardware.
Kim recalls: “One story from early on in our partnership highlights the important role Trelleborg played. Analysis on a Zurcon® engineered plastic seal, a standard material for applications such as ours, showed that CO2 was forming carbonic acid somewhere inside the compressor. This caused the stainless steel in the equipment to rust and build a black slurry, which was damaging the seals. The discovery led us to add additional filters to the system to make the equipment run cleaner.”
Trelleborg and Dalum collaborated through several rounds of modifications, testing seals and making other adjustments to the hardware in the compressor. The seals were carefully matched to the application environment, which changed with each adjustment made. When the operating temperatures within the compressor increased, Trelleborg helped to identify a new material that would withstand more extreme conditions. Turcon® FoodPro® MF6 proved to be the best material for our application, ensuring CO2 remains in the compressor as the pressure and temperature rises.
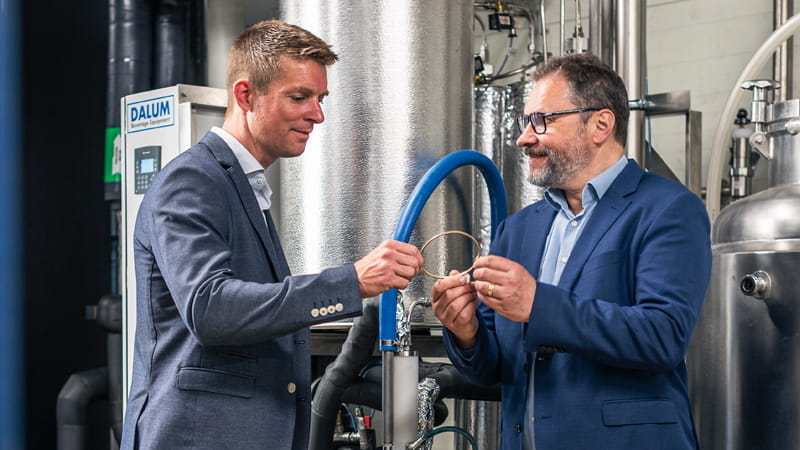
Mikkel Moerup, Global Segment Director, Food, Beverage & Potable Water, shares the Trelleborg side of the story, “When we received Kim’s inquiry to collaborate with him on a system to capture and compress CO2, we knew immediately that this would be a rewarding project. We were encouraged to use our full breadth of expertise on sealing technology to test, analyze and create the optimum sealing solution for his equipment. The path was not an easy one, but together with our team at the Customer Solution Center Denmark and colleagues at the manufacturing site in Helsingoer, we were able to meet the challenge.”
Kim’s CO2 Recovery Plant is an especially challenging application for seals and sealing materials. The seals had to satisfy several requirements:
- CO2 is compressed in a dry application. Without lubricants, the seal must demonstrate high dimensional stability and low friction to ensure smooth performance and prevent friction and wear.
- As the CO2 was being compressed, the temperature in the compressor raised to a high level. Initially, a Zurcon® FoodPro® engineered plastic was tested in the system, but higher temperatures were a challenge. It was clear that a Turcon® FoodPro® PTFE was required.
- Sealing materials must meet government compliance requirements and industry guidelines for food contact materials (US Food and Drug Administration (FDA CFR 21), EU (Reg. EC 1935/2004), and Chinese National Standards (GB 4806.1-2016, GB 4806.11-2016, GB 9685-2016)).
Materials and seal designs were tested in parallel to identify the optimum solution. The sealing solution devised for the CO2 recovery plant consists of Turcon® Glyd Ring® APG for the compressor pistons and Turcon® Slydring® GM for the linear bearings.
The Turcon® Glyd Ring® APG is characterized by a relatively small sized Turcon® ring, compared to the energizing O-Ring, which offers maximum flexibility and effective sealing performance at very low pressures. The saddle design of the Turcon® ring protects the O-Ring. Turcon® FoodPro® MF6 was identified as the material of choice for both seals due to its superior performance in the application environment and its compliance with all major food contact regulations.
How the CO₂ Recovery Plant works
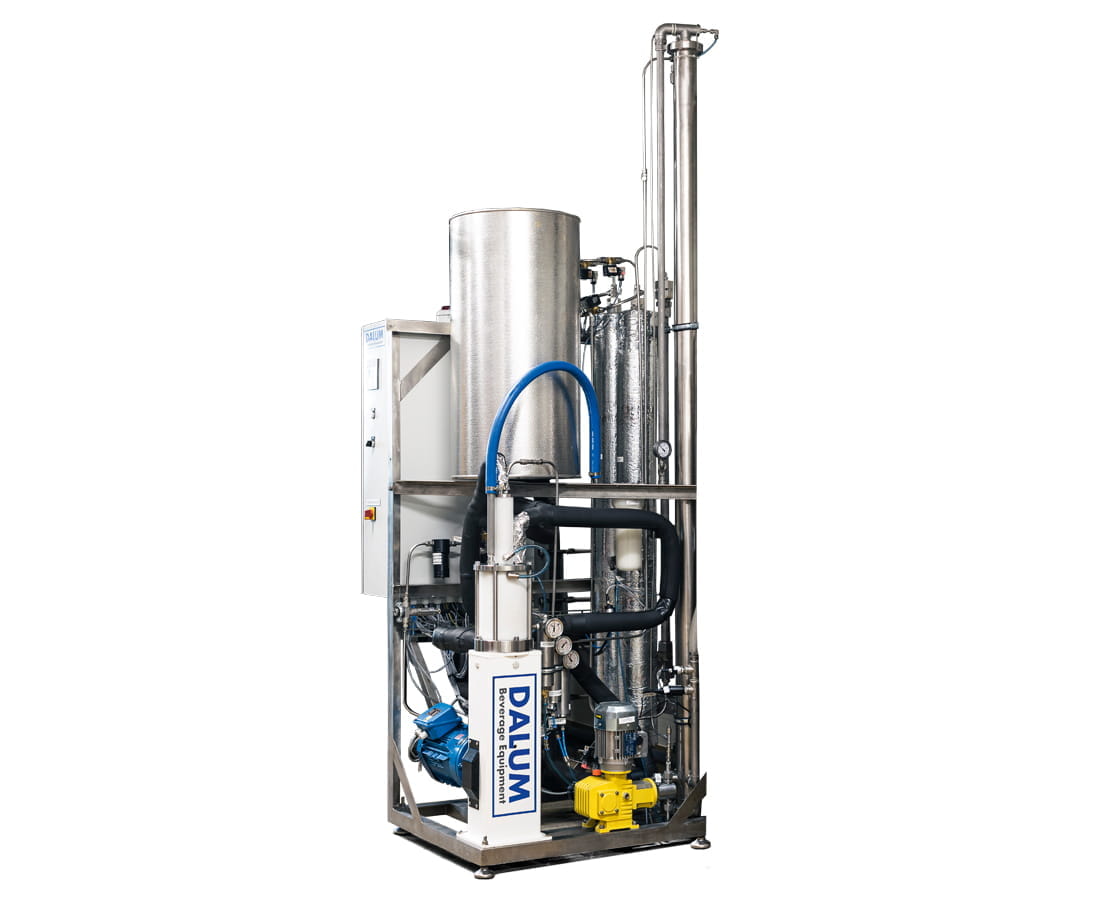
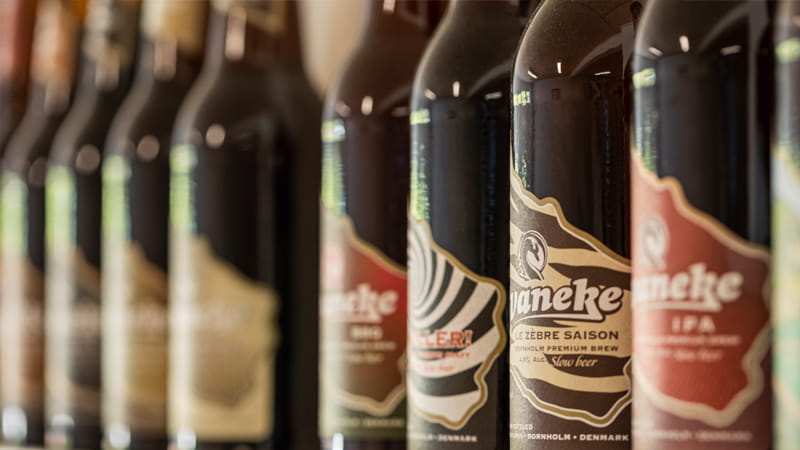
Svaneke Bryghus is on the Danish island of Bornholm and for many years, it has worked with sustainable initiatives. More recently, they moved to 100% organic ingredients in 2018, and established a canning in 2019. In 2020, the next goal was to brew, bottle and tap CO2 neutral, which was achieved with the carbon capture equipment from Dalum Beverage Equipment.
Jan Paul, Brewmaster at Svaneke Bryghus explains, “you add carbon dioxide when the beer is bottled, but at the same time, carbon dioxide is formed when the beer ferments. We brew about 17,000 hectoliters of beer per year, the equivalent of 3.4 million half-liter bottles, and this produces approximately 72 tons of CO2, which can now be recycled during the filling process.
Jan continues, “Kim Dalum loves to innovate and so do I. Working with him to co-create a piece of equipment made sense. Because of Kim’s deep insight into the world of brewing, we formed a unique partnership to optimize Svaneke’s brewing process.”
Game Changer – Marking a Milestone
Since the beginning of the year, all beer at Svaneke is brewed CO2 neutral. This milestone has been marked with a new beer called Game Changer.
Alongside the new title, the carbon capture equipment has had a positive impact in other ways. Jan says, “less CO2 in the brewery improves the working environment as well. ‘CO2 headaches’ are not unfamiliar to brewers as the gas normally escapes the process. When CO2 is captured this problem is gone. Also, Svaneke condensates and captures other fumes from the fermentation thereby eliminating the smell that often spreads to the brewery’s surroundings. This is very positive for our neighbors.”