材料
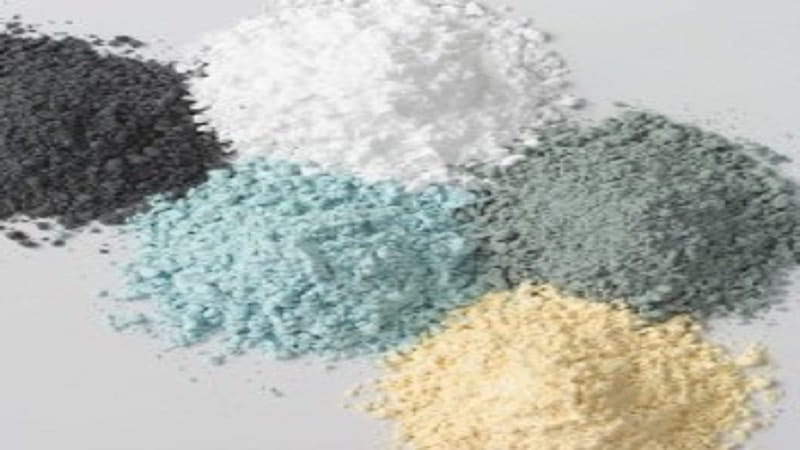
憑藉數十年的經驗,與全球領先的設備製造商和最終用戶合作,我們開發了一系列非常適合汽車應用的材料。 從基本的彈性體等級到領先的高規格化合物; 我們的創新密封材料有助於優化性能,同時確保密封完整性。
汽車行業的具體材料問題
趨勢 - 議題- 發展
燃料變化 - 生物燃料比傳統燃料對彈性體的侵蝕性更強 - 耐生物燃料材料
排放法規變得更加嚴格 - 減少顆粒物和 NOX - 選擇性催化還原材料 (Adblue)
需要更高的效率 - 更高的溫度和壓力 - 能夠承受極端溫度的材料
Ethylene Acrylate Rubber (AEM)
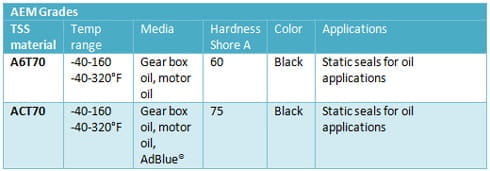
AEM is resistant to oil, heat and ozone. It exhibits good resistance to lubricating oils and greases (mineral or synthetic based containing aggressive additives), transmission/power steering fluids, water up to 100°C/212°F and in special circumstances also to dry and wet sour gases and blow-by. The operating temperatures for AEM range from -40°C/-40°F to 160°C/320°F, and for a short period of time up to 190°C/374°F. AEM closes the gap between HNBR and FKM.
The material has:
- Excellent weather & ozone resistance
- Very good heat resistance
- Low compression set
- Resistant to most oils, greases (even with aggressive additives)
- Good low temperature properties
Applications:
Typical applications for AEM are all kind of static seals in contact with oil as it happens in gear boxes, oil pumps, cam covers or others. Special formulations allow the usage in contact with AdBlue®.
Products:
- ECUs for gear boxes, cam cover & oil pan gaskets.
- AdBlue® injectors or QC’s
Ethylene Propylene Diene Rubber (EPDM)
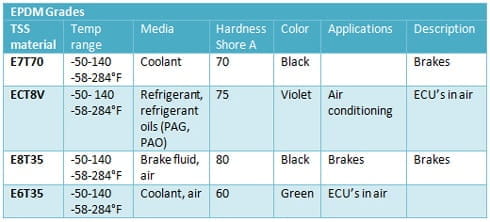
Due to the saturated polymer chain, EPDM offers very good heat, ozone and ageing resistance. In addition it also exhibits an excellent low temperature behavior, as well as good insulating properties. The operating temperatures of applications for EPDM range from -45°C/-49°F to 150°C/302°F, and for a short period up to 175°C/347°F (with sulfur-cured types the range is reduced to 130°C/266°F).
The material has:
- Excellent resistance to weather & ozone
- Excellent resistance to phosphate esters
- Good resistance to oxidising chemicals (acids) and brake fluids
- Low swelling in water
- Outstanding resistance to hot water & steam up to 180°C
- Good heat ageing properties
- Excellent low temperature properties
Applications:
EPDM is typically used in applications with brake fluids (based on glycol), as radiator gaskets in contact with coolant, as O-rings in air conditioning to seal refrigerants or just as dust seals.
Products:
O-rings, gaskets
Fluorocarbon Rubber (FKM)
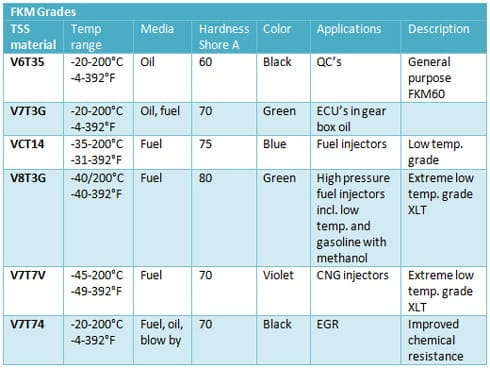
In automotive applications, FKM is known in particular for its very good resistance to fuel, oil and aggressive media as well as the excellent resistance to ozone, weathering and ageing. Depending on structure, fluorine content and used curing system FKM materials can differ with regards to their chemical resistance and cold-flexibility. The operating temperature of FKM ranges from -20°C/-4°F to 200°C/392°F, for a short period of time up to 230°C/446°F.
Special FKM grades can be used down to -45°C/-49°F.
The material has:
- Resistance to oil & grease
- (problematic additives!)
- Very good resistance to fuels
- Excellent heat resistance
- Excellent weather & ozone resistance
- Good acid resistance
Applications:
Due to high chemical resistance and low swelling in fuels (especially when containing ethanol and methanol) FKM can typically be found in the complete fuel supply chain (fuel injectors, quick connectors, high pressure pumps, etc.). Additionally, gaskets in ECUs for gear boxes are also a field of application.
Products:
Fluorosilicone (FVMQ)
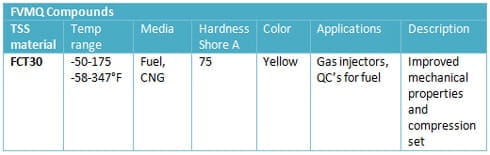
FVMQ (Fluorosilicone) has a good heat resistance, very good low temperature flexibility and excellent resistance to weather, ozone and UV rays. FVMQ offers a significantly better chemical resistance than standard silicones (VMQ) especially when used with hydrocarbons, aromatic mineral oils and fuels. Compared to VMQ the temperature range is slightly reduced from -50°C/-58°F to 180°C/356°F.
The material has:
- Very good chemical resistance
- Very good resistance to fuel and oil
Applications:
The main applications for this material are injectors for CNG and quick connectors for fuel rails
Products:
Mainly O-rings, membranes
Hydrogenated Nitrile Butadiene Rubber (HNBR)
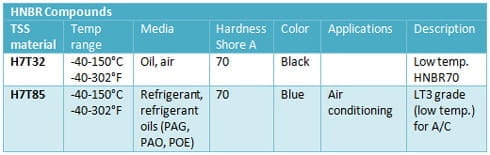
HNBR is made via selective hydrogenation of the NBR butadiene groups which improves the temperature and ozone resistance considerably. Due to the polymer structure, HNBR offers both resistance to polar and nonpolar media. The selection for dedicated automotive applications depends on the ACN content which can range from 18% to 50% (this influences the swelling in oil), as well as on the degree of saturation (this influences the heat resistance). HNBR offers extraordinarily good mechanical properties and abrasion resistance. The operating temperature ranges, when in contact with mineral oils and greases from -30°C/-22°F to 140°C/284°F and for a short period of time up to +160°C/320°F. Special types can be used down to -40°C/-40°F.
The material has:
- Superior heat resistance up to 140°C
- Superior environmental resistance
- Improved resistance to polar fluids
Applications:
Due to the good abrasion resistance and oil resistance, the main applications are actuator seals for gear box applications. In addition, HNBR is often used in air conditioning applications.
Lip seals, O-rings, static seals
Nitrile Butadiene Rubber (NBR)
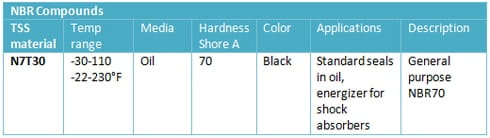
As with HNBR the properties of Nitrile Rubber (NBR) depend mainly on the ACN content which can range from 18% to 50%. In general NBR shows pretty good mechanical properties. Due to the unsaturated polymer chain the maximum operating temperature is limited to +100°C/212°F (for a short period of time up to 120°C/248°F), while the minimum temperature can go down to -30°C/-22°F (suitable formulated NBR can be used down to -50°C/-58).
The material has:
- Good oil resistance
- Moderate heat resistance, 125°C in oil / 100°C in air
- High tensile & tear strength
- Good abrasion resistance
- Non expensive
Applications:
NBR is widely used in contact with mineral based oils and greases as energizers for PTFE seals or in shock absorbers due to the excellent abrasion resistance.
Products:
Silicone (VMQ)
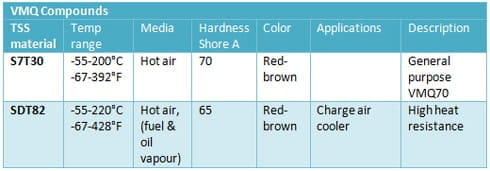
Due to the different polymer composition VMQ (Silicone) shows excellent heat resistance combined with an extraordinary cold flexibility and a very good resistance to weather, ozone and UV rays. Specific formulations are resistant to aliphatic engine/gear oils and water up to 100°C/212°F. The suitable operating temperature ranges from -60°C/-76°F to 200°C/392°F (special grades up to 220°C/428°F).
The material has:
- Very good low and high temperature properties
- Excellent resistance to weather and ozone
Applications
Due to their heat resistance they are used as heat exchanger gaskets
Products:
Turcon® M12: High performance PTFE
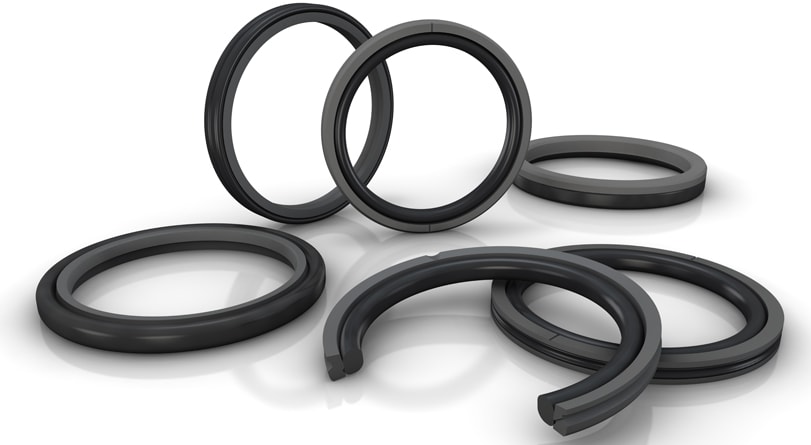
Turcon® M12 from Trelleborg Sealing Solutions is a PTFE based sealing material whose performance is unrivalled in key hydraulic sealing characteristics, such as friction, wear and high pressure operation.
Comprehensive testing has shown that no other PTFE based material can give such universally exceptional performance.
Turcon® M12 is now recommended by Trelleborg Sealing Solutions as the material of choice for a wide variety of automotive hydraulic applications including:
- Cylinders for convertibles
- Shock absorbers
- Active body control
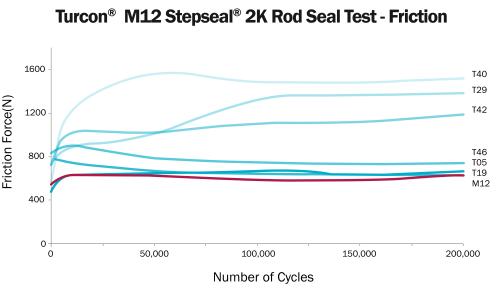
- 避免表面上劃傷
- 低摩擦力使運動平穩
- 承受高系統壓力
- 出色的耐磨性
- 良好的抗擠壓性
- 耐受幾乎所有介質,包括各種潤滑劑
- 延長密封壽命
該圖顯示了在同一測試室中彼此相對放置的兩個密封件的摩擦特性。 Turcon® M12 的摩擦力約為 T40 摩擦力值的一半。 這些測試結果證明 Turcon® M12 具有最低且最一致的摩擦特性。
XLT Materials
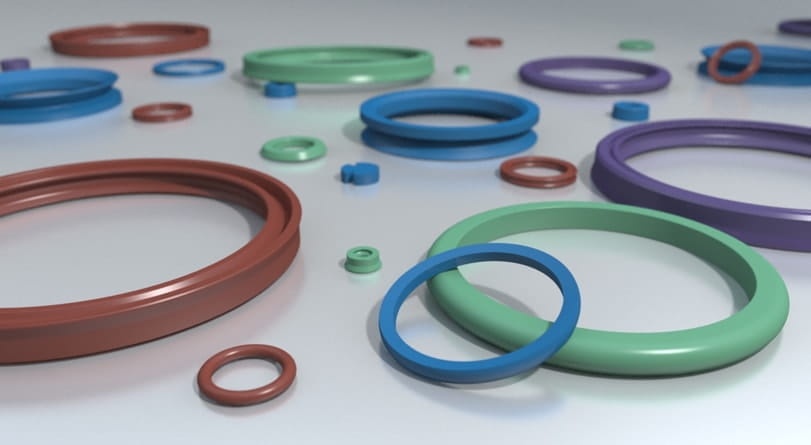
The XLT family is the latest innovative series of low temperature peroxide-cured fluoroelastomer grades from Trelleborg Sealing Solutions. XLT has been designed to specifically meet the challenging demands of automotive applications and is useful within high pressure direct injection applications.
Automotive trends affecting elastomer sealing materials
- Fuel changes – Materials need to be resistant to bio-fuel that are more aggressive to elastomers than traditional fuels.
- Stringent emission regulations – Seals must withstand different media, such as Adblue, used for selective catalytic reduction.
- Greater efficiency – Materials must be resistant to a wider temperature range and pressure extremes.
- Retraction (TR10) values ranging from -30 °C to -45 °C / -22 °F to -49 °F
- Increased chemical resistance especially against aggressive ethanol and methanol fuel mixtures
- Increased sealing capability in aggressive environments, for example, in engines
- Excellent retention of mechanical properties
High pressure direct fuel injection
Testing of the new generation XLT materials in bio-fuel applications has proven that this family of materials outperforms and extends the temperature performance capability of traditional fluorocarbon elastomers, with comparably low volume swell and good retention of physical properties. They also demonstrate excellent chemical resistance against most media including more aggressive ethanol/fuel and methanol/fuel mixtures.
Optimized low temperature behavior
With TR10 values reaching - 45 °C /- 49 °F, excellent sealing capability is achieved, outperfoming other fluorocarbon elastomers.