Enter the HybridAccelerator – A story of how two became one
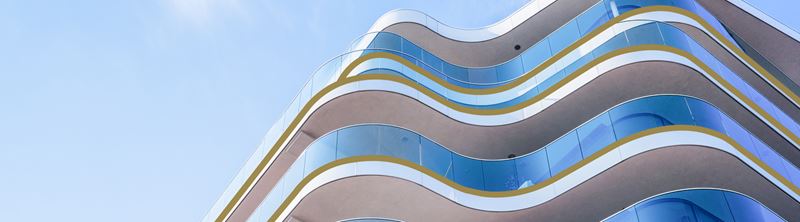
For Trelleborg’s Seals & Profiles operation, there is no such thing as impossible. Our Innovation Team set itself the challenge of combining EPDM and silicone as part of a single, unique sealing system – a task that had never been done before.
With rapid digitalization and the emergence of circular building methodologies, the building and construction sector has been a hotbed of innovation in recent years. In today’s resource- and environmentally conscious market, architects and planners are under pressure to make buildings as efficient and sustainable as possible, while keeping a close eye on aesthetics.
Big breakthroughs often arise from small adjustments; the discovery of a new material unlocks the door to a more efficient way of working, for example. But gasket technology is different: the right materials are often available, but they are not being used in the most effective way.
Wanted: the best of both worlds
Ideally, a door or window seal offers the best of both worlds. First, it has a high level of flexibility and a good compression set to cushion the edge of the door or window and ensure a good opening and closing motion. Second, the gasket needs a strong, rigid base that inserts easily and firmly into the door or window frame to provide a reliable, watertight seal.
Silicone, a highly flexible material, meets the first requirement. However, it is too soft to support the rigid base of the gasket structure and provides limited resistance to temperature and climatic conditions. In contrast, ethylene propylene diene monomer (EPDM), a dense synthetic rubber, offers a strong, rigid structure, but none of the flexibility or maneuverability of silicone.
The perfect solution would be to combine the two materials. Yet, according to prevailing expert opinion, EPDM and silicone are incompatible materials that cannot be effectively bonded.
“It’s like trying to combine oil and water,” explains Per Arnqvist, Product Development Manager at Trelleborg Seals & Profiles. “The two chemistries just don’t speak to each other. Most of the time, you end up with a weak bond, so there’s a high risk of the materials coming apart.”
Most conventional sealing systems use additional adhesives and plastics to join the separate components of the gasket. This makes installation more difficult and raises challenges from a sustainability perspective. Furthermore, different combinations may be required depending on the type of application, for example if the opening is in the building interior or exterior. This can add further complexity to the planning and design process.
Time for a new approach
Drawing on its extensive track record in seals and profiles technology, Trelleborg decided to tackle this long-standing challenge from a new angle. Our Innovation Team set out to create a unique hybrid design that took advantage of the unique qualities of silicone and EPDM in the best possible way.
“Our philosophy is always using the right material in the right place,” says Arnqvist. “Rather than develop a brand-new compound, our idea was to create a single system that leveraged different material properties in different parts of the gasket.”
Trelleborg’s HybridAccelerator solution uses EPDM as the base polymer to create the hard ‘foot’ of the seal that slots into the window or door frame. Meanwhile, the soft ‘head’ or ‘bubble’ of the gasket is made of silicone to provide the desired cushioning effect. The two components are joined seamlessly during extrusion to form a connected piece of material, with no risk of a tear-off effect.
The key lies in the vulcanization process. By making small, incisive adjustments to its curing system over a number of months, Trelleborg’s Innovation Team was eventually able to achieve a secure bond between the two materials. The resulting hybrid was stress-tested over 350,000 test cycles. This proved the solution has a high level of fatigue resistance, with no identifiable changes in the bond detected. The hybrid also demonstrated excellent resilience to external stressors, including wide-ranging temperatures and weather conditions.
Unlocking synergies
Trelleborg’s EPDM-silicone HybridAccelerator solution meets the dual demands of modern sealing technology: the need for firmness and flexibility. For end users, this means the best of both worlds. The gasket’s hard EPDM component offers easier and safer groove installation. A further benefit is optimized handling, including the possibility of self-adhesive options.
Meanwhile, the use of silicone in the gasket’s head significantly increases the functional range of the system. It also enables greater design freedom; through successful trials, our hybrid has been shown to be compatible with thin layer technology (TLT). This opens the door to customization, giving end users the possibility of complex shapes. Furthermore, silicone’s high UV stability means seals can be designed in custom-made colors and blends.
Long-term potential
This unique combination of reliability and flexibility offer advantages for multiple end-user markets, including the demanding, fast-changing world of building and construction.
As well as doors and windows, Arnqvist believes Trelleborg’s EPDM-silicone hybrid can add value to various other applications, including facades. “Facade seals have traditionally presented a challenge,” he explains. “Most of the current workarounds involve significant use of silicone glue and plastics; we hope to offer end users a far more efficient and sustainable solution.”
In an era of fast change and even faster results, a solution to this age-old problem has been a long time coming. But, as the saying goes, good things come to those who wait.
For more information on Trelleborg’s HybridAccelerator solution and its advantages, please contact gold.standard@trelleborg.com.