FrictionControl – How Trelleborg is opening the door to new opportunities
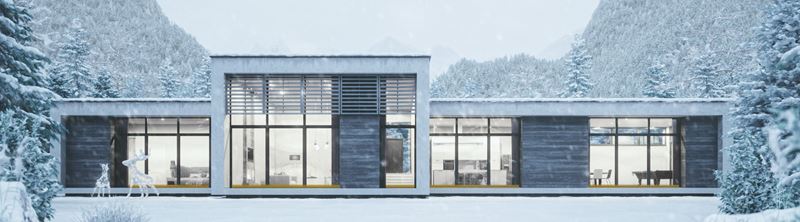
At Trelleborg Seals & Profiles, we are always looking to push the boundaries of what is possible in industrial design. One of our latest innovations – Friction Control – is changing the game for a specific class of applications, including sliding doors and windows, roller shade guides, and door profiles.
Mind the gap
As the mantra goes: there are no problems, only solutions. But some take longer to find than others. Sliding applications, such as windows and façades, have long presented manufacturers with a dilemma: how to tightly seal the gap between two surfaces without compromising the functionality or durability of the application.
While various sealing options are available on today’s market, including sliding lacquers, brush gaskets, and flock profiles, these solutions inevitably involve a trade-off.
“Any movement between two parts creates friction,” explains Bernhard Haaß, Profiles Design Manager for the EMEA region at Trelleborg Seals & Profiles.
“In a sliding door, for example, there is constant friction between the gasket and the underlying surface you are sealing toward. This usually means there is a compromise. Generally, the better the sliding properties, the worse the sealing properties. On the other hand, the better the sealing properties, the more sensitive the system is to abrasion.”
The doormaker’s dilemma
Abrasion creates challenges for the application owner. Because common elastomer materials such as Ethylene Propylene Diene Monomer (EPDM) offer limited resistance to abrasion, the gasket is quick to degrade. To reduce the handling forces and avoid the need for frequent replacements, designers may seek to limit contact between the gasket and the sliding element of the application to only a small part of the sliding movement, limiting overall functionality.
These limitations often rise to the surface in technical applications. To be accessible by wheelchair, an entrance requires a low threshold of no higher than a few millimeters. This makes it difficult to seal the gap between the threshold and the lower edge of the door.
Due to the high friction and the resulting damage to the rubber, it is almost impossible to open and close the door using a standard gasket. But the alternative device, a brush gasket, has a reduced sealing effect.
More tonnage, more problems
In the fast-evolving world of industrial design, applications such as sliding door façades continue to become bigger and heavier, putting increasing pressure on these already sensitive systems.
Meanwhile, larger projects now rely on the chemical bonding of different materials. This creates further complexities, namely the risk of a tear-off effect between the different materials because of high handling forces.
The problem gets worse for industrial-scale systems, such as floodgate fenders and dock fenders. In such cases, the poor durability of the component parts leads to frequent large-scale repairs and replacements, at significant cost and inconvenience to infrastructure owners or local authorities.
It all links back to the materials themselves: if the elastomers in use are unable to cope with the handing forces or abrasion, then the application itself will always be compromised.
Finding the right combination
However, while every material has certain inherent limitations, it is often possible to circumvent these by combining different materials with complementary properties.
“When it comes to product development, our philosophy is ‘the right material to the right place’,” says Haaß. “By combining the unique properties of different materials, we are able to find the right solutions for specific technical challenges.”
This is where Trelleborg’s knowledge of elastomer and thermoplastic materials comes in. Through extensive research and development, our seals and profiles operation has developed a new approach to meet the twin demands of abrasion resistance and sliding. The answer lies in a high-molecular polyethylene, Ultra-High-Molecular-Weight Polyethylene (UHMW-PE).
UHMW-PE has a very low coefficient of friction, making it significantly more resistant to abrasion than synthetic rubbers commonly used in gaskets. And because the material can be produced in a wide range of thicknesses, ranging from 0.1 mm to 0.2 mm, it can be applied to the underlying EPDM gasket as a thin foil or film. UHMW-PE combines perfectly with EPDM during vulcanization to create a tight chemical bond without the risk of a tear-off effect.
The best of all worlds
Thanks to this unique new compound, Trelleborg’s Friction Control solution offers outstanding abrasion resistance compared with other materials, including steel, enabling excellent sliding properties. Furthermore, our solution offers excellent resistance to extreme temperature and climatic conditions, as well as chemicals, making it well suited to harsh weather conditions and industrial environments.
In turn, increased durability means less consumption of raw materials. As well as offering advantages from a sustainability perspective, this also means fewer repairs and reduced maintenance, enabling time and resources to be channeled into new designs.
Just as important, the functionality of the wider application is improved. Reduced friction between the gasket and the sliding element means the end user requires less handling force to slide the door or façade along the gasket. The gasket can also make contact during the entire sliding movement, without risk of damage.
Opening the door to new applications
With Friction Control offering an answer to these recurring technical problems, manufacturers can enjoy greater flexibility in their designs. This means the freedom to develop larger and more complex applications without having to compromise on functionality or durability.
Haaß concludes: “We hope our solution will open the door to new, customized innovations with excellent sliding functionality and high abrasion resistance. From sliding doors and windows to gates, roller shutter guides, threshold seals, and industrial automated garage doors, the possibilities are endless. Watch this space.”
For more information about Friction Control, get in touch with Trelleborg today at gold.standard@trelleborg.com.
Bernhard Haaß, Design Manager Seals & Profiles