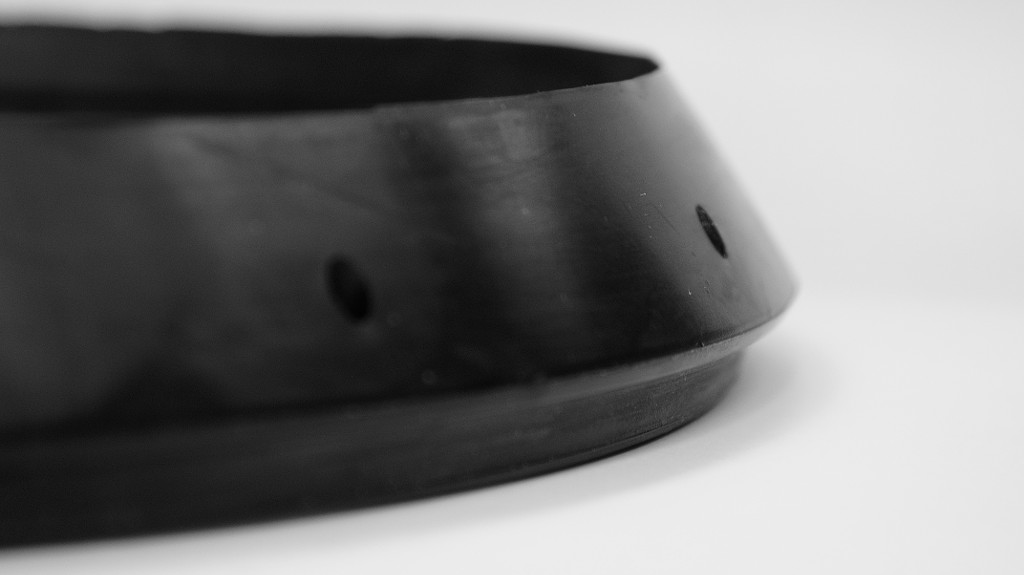
Seal design & function
Rieber Pressure seals are integrated into the pipe during the manufacturing process. It uses the mandrel together with the seal as a tool to form the pipe socket. This ensures that the seal always remains in the correct position in the join.
The seal is equally effective under both positive and negative pipe pressure (vacuum). Under positive pressure, the higher the pressure the greater the sealing force. Under vacuum, the seal maintains a positive sealing force against spigot and socket, preventing sand or soil to enter the joint.
Rieber Pressure seal is a composite seal consisting of a flexible rubber element to seal effectively against spigot and socket and a treated metal insert which holds the seal firmly in place.
The seals are designed for PVC pipes in compliance with ASTM 41.
Sizing Chart
PIPE SIZE (mm) | A (mm) | B (mm) |
100 | 12.5 | 27.3 |
450 | 28.8 | 59.5 |
500 | 32.0 | 68.5 |
630 | 36.0 | 77.0 |
800 | 42.0 | 92.0 |
900 | 98.4 | 46.0 |
1000 | 107.0 | 50.0 |
1200 | 119.8 | 56.0 |
PIPE SIZE (Inch) | A (Inch) | B (Inch) |
4 | 0.512 | 1.099 |
6 | 0.591 | 1.264 |
8 | 0.669 | 1.433 |
10 | 0.788 | 1.689 |
12 | 0.869 | 1.854 |
14 | 0.944 | 2.02 |
16 | 1.06 | 2.269 |
18 | 1..142 | 2,444 |
20 | 1.26 | 2.696 |
24 | 1.418 | 3.034 |
30 | 1.575 | 3.37 |
36 | 1.575 | 3.37 |
42 | 2.047 | 4.381 |
48 | 2.047 | 4.381 |
PIPE SIZE (Inch) | A (Inch) | B (Inch) |
1-1/2 | 0.315 | 0.673 |
2 | 0.315 | 0.673 |
2-1/2 | 0.433 | 0.929 |
3 | 0.472 | 1.012 |
4 | 0.512 | 1.099 |
5 | 0.551 | 1.181 |
6 | 0.590 | 1.264 |
8 | 0.669 | 1.433 |
10 | 0.787 | 1.689 |
12 | 0.869 | 1.854 |
14 | 0.944 | 2.020 |
16 | 1.060 | 2.269 |
18 | 1.142 | 2.444 |
20 | 1.210 | 2.696 |
24 | 1.418 | 3.034 |