Challenge
Develop a disposable sleeve for a surgical instrument
- A customer wanted to improve the design of a medical device used to cut and cauterize tissue in minimally invasive surgeries
- The goal was to make the device reusable by creating a disposable, biocompatible, flexible sleeve cover for the surgical instrument
- The new sleeve needed to be thin (0.55 mm), resistant to tearing and heat, reduce coefficient friction, provide ease of installation and removal, and maintain physician mobility
- Other companies proposed a silicone compound that lacked consistency and durability jeopardizing the effectiveness and integrity of the surgical procedure and clinical outcomes
Solution
Collaborate to optimize the chemical properties of the material
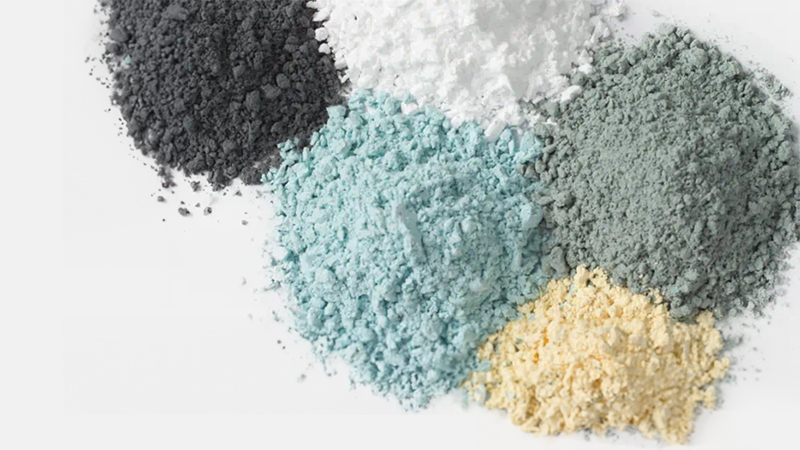
- Trelleborg’s product and material science engineers collaborated with the customer’s technical team to optimize the material’s chemical properties
- To meet the heat resistance need, they selected fluoroelastomer (FKM)
- To address the difficulty of creating a thin cross section from FKM, the team developed two materials with three hardness ranges for customer evaluation and performance analysis testing
- Variations in the material modulus across the two material sets provided a range of resistance options to evaluate tactile feel
- A surface coating was added to address the low friction requirement for ease of installation to the instrument
Results
A material that met the customer’s needs in every setting.
- Nine sample configurations were evaluated and adjusted to deliver the final high-performance sealing solution
- The custom-formulated compound delivered a 277 percent increase in tear strength and 287 percent increase in elongation, demonstrating significantly improved resilience
- The customer selected Trelleborg to take the product through prototyping and production
- The solution’s value proposition for surgeons increased by improving clinical outcomes and lowering total cost of ownership