Passing the taste test
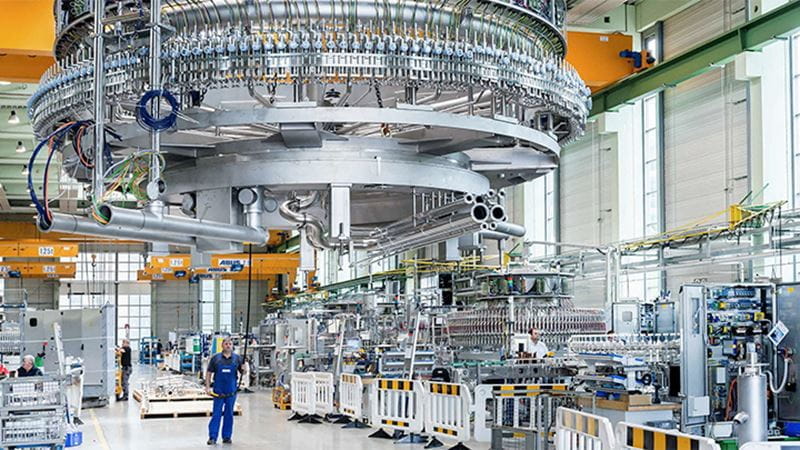
Trelleborg partnered with filling specialist Krones. Part of the successful outcome is a completely new aroma-resistant sealing material.
Walk into any supermarket or convenience store and you’ll find an abundance of choices in the beverage section, with rows of energy drinks, sodas and juices. Even water is no longer just natural but often flavored to satisfy any taste or preference.
This multitude of alternatives is great for the thirsty, but our desire to try the new and tasty has created a challenge for beverage producers and the bottling industry. The trend toward flavored drinks has put new focus on the issue of aroma carryover from one beverage to another after changeover in the filling process. Beside the risk of wasting hundreds of liters of beverages, aroma migration can cause unwanted downtime, extra monitoring, and consumer complaints. In the worst case scenario, it can even lead to fines or result in barring products from sale.
“Flavor migration is a risk that must not be underestimated, particularly when intense aroma compounds are used,” says Dr. Eva Beierle, Development Engineer Aseptic and Process Technology at German packaging, and bottling machine manufacturer, Krones. Beierle sees great benefits from Trelleborg’s newly developed aroma-resistant sealing material, as it offers its customers increased production flexibility.
Everyday millions of glass bottles, cans and plastic containers run through Krones’s bottling lines all over the world. Many plants produce a variety of drinks and greater variety means shorter production times, and more changeovers, which despite rigorous cleaning processes increase the risk of aroma carryover. To tackle the issue and investigate exactly where and why aroma carryover occurs, Krones partnered with Trelleborg Sealing Solutions.
“By combining Krones’ expertise in beverage trends and development with Trelleborg’s expertise in elastomer sealing materials, we found that the type of elastomer materials used in the machine’s sealing components is a significant factor in aroma carryover,” says Tim von der Bey, Project Manager for the collaboration project at Trelleborg.
A large filling machine can have up to 3,000 different seals. Pipes, heat exchangers, valves —all of them require seals to connect parts, control pressure and add the right amount of beverage to each unit. Frequent seal changes are costly and time consuming, putting strains on flexibility. Hence, step one was to discover what type of seal would be most sustainable and best suited for different types of beverages.
For nearly two years the Trelleborg lab in Stuttgart, Germany, hosted rigorous testing of the most commonly used elastomers in the bottling industry.
Different types of sealing materials were exposed for weeks, and in some cases even months, to everything from aromatic fruit juice and cola-flavored sodas to vodka, detergents, and curry-spiced tomato ketchup.
The aim was to determine the susceptibility to flavor migration, as well as the durability of sealing materials when exposed to heat and to the cleaning chemicals used in the industry. Simultaneously, Krones’ R&D Lab in Neutraubling, Germany, evaluated flavor migration through both gas chromatography and human test panels.
“To measure the amount of aroma that migrates, the exposed sealing materials were left in water for different periods of time,” Beierle says. “Then we let a group of 20 to 30 people evaluate and rate the water.”
The result: both good news and bad news. The good news is it gave new in-depth knowledge about how different types of elastomers behave when exposed to strong flavors, heat, and cleaning chemicals. This information now helps customers choose the most suitable seal.
The bad news is that the most commonly used sealing material in the food and beverage industry, EPDM (ethylene propylene diene monomer rubber), turned out to be the most susceptible to aroma carryover, increasing the risk of flavor migrating from one drink to another. On the other hand, EPDM had the best chemical resistance and durability against cleaning agents.
FKM (fluorocarbon) also performed well in terms of chemical resistance, but for aroma carryover the results changed depending on the beverage. Apple flavored water, for example, tended to damage the FKM seals.
“Best-in-class were seals made of FFKM(perfluoroelastomer), such as the Trelleborg Isolast® FoodPro® compounds,” says Martin Krüger, Area Sales Manager responsible for food and beverages at Trelleborg Sealing Solutions. “The Isolast materials did not absorb aromas and showed virtually no detectable effect on the taste of subsequent beverages.”
The research concluded that there is no perfect seal compound on the market suitable for every use. For many lightly flavored beverages, EPDM is a suitable material, especially since high temperatures are often necessary in the production process. Isolast is the ultimate for sealing in food and beverage applications, but with a higher cost, may be overengineered for some processing. To help guide customers, Trelleborg created a new tool to find the best match.
We have reinvented the way we provide information on sealing materials by creating a customer tailored software-as-a-service solution,” von der Bey says.
Based on the type of beverage and the cleaning agents, the new software shows which seal compound is the best match for certain beverages.
“Selecting the optimum sealing material is critical in preventing aroma carryover and certainly has a positive impact on both our customers and those of Krones,” von der Bey says. “But we did not want to stop at that. Our findings resulted in the development of a completely new and superior aroma-resistant sealing material.”
“With the new compound we have a sealing material that is both affordable, durable and low in flavor migration,” Beierle says. “It’s a huge benefit to be able to tackle the drawback of all the other compounds and at the same time optimize one that is perfect for the beverage industry.”
The new compound will be available at first for Krones’s customers exclusively.
This is an article has been reproduced from Trelleborg's T-Time magazine. To download the latest edition, go to: www.trelleborg.com/t-time