The Wild West of Fender Vendors
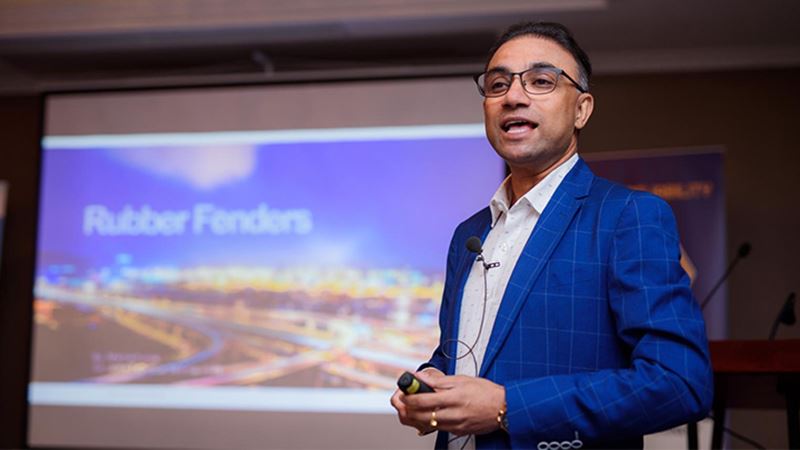
Image: Mishra Kumar, Business Unit Director - R&D at Trelleborg Marine & Infrastructure
Fenders may not hold the glamour of digital technologies, but they are still part of smart operations for ports and ships. If a fender fails during a collision or heavy berthing, it can be hugely damaging to a company’s performance, profitability, and reputation.
At a time when environmental responsibility is paramount, these unassuming systems can also be the front line for preventing oil spills, especially if oil tankers experience a heavy berth.
For ports, inferior fender performance can result in incidents or damage that can cause significant downtime and berth under-utilisation, costly insurance claims and repairs, injuries, and dissatisfied customers.
Fenders are usually selected in good faith and it’s only when port operators hear on the grapevine about incidents at other ports, that experts are brought in to test their own performance. For example, prior to undertaking upgrade works, extensive testing at the Davao International Container Terminal in the Philippines revealed that the performance of their existing fender structure was unable to guarantee the load-bearing requirements of existing reefer vessels. This investigation was driven by reports that another port in Davao had upgraded its berth using poor quality fender systems that had cracked and corroded within months of installation.
When thinking about budgets, choosing the lowest cost option for fender systems can be a false economy. Aside from being a potential operational liability, cheaper products might only last two to three years. In contrast, high quality systems developed and implemented by providers who can advise on lifecycle issues can last for around 20 years. Care should be taken with detailed fender system design, fender production and quality control, installation, operations, and maintenance.
Importantly, despite its common use, the term ‘rubber’ is quite ambiguous, as it covers a variety of types and grades. For example, it can be natural, synthetic or a blend. Different types of rubber are suitable for different applications. Natural rubber has a much lower velocity factor, and an increase in reaction force at high-speed compression compared to synthetic (styrene-butadiene) rubber. Blended ethylene propylene diene rubber is ideal for high temperatures, and synthetic rubber shows lower crack growth. Designing an effective rubber fender for the conditions of a specific site therefore requires a thorough understanding of rubber type and its effect on a fender’s base performance factors such as force and temperature.
However, no guidelines for quality control practices are followed when selecting, specifying or determining rubber type for a fender. This lack of specification can mean that manufacturers use different types of rubber, including low-quality recycled rubbers, to minimise costs while designers remain unaware that the product might not deliver the desired performance for an application.
A lack of rigorous, independent testing and standardised certification is exacerbating the issue. It is still acceptable for manufacturers to conduct their own performance tests and self-certify products. This conflict of interest and lack of standardisation means that customers have no benchmark or third-party quality assurance regarding the design and components of fenders.
The situation has led to a disparity between ports that implement strict guidelines, such as many in Europe, and those in developing markets where there can be no requirements at all. As a result, vessel owners and operators are facing varying risks to the safe berthing of their ships depending on which ports they visit.
New, rigorous testing processes need to be standardised with input from credible certification bodies. This needs to be prioritised in guidelines such as those provided by PIANC, the revision of which is a work in progress. However, unlike BS 6349, the PIANC guidelines aren’t enforceable for manufacturers, so port authorities, operators and marine engineers need to hold fender designers and manufacturers accountable by demanding that best-in-class testing, and design standards are met.
If mindsets and standards shift, there is a real opportunity to unlock innovation for improving port resilience and ship safety from even these unassuming assets – it’s time to tame the Wild West.