A whole system approach to fender performance
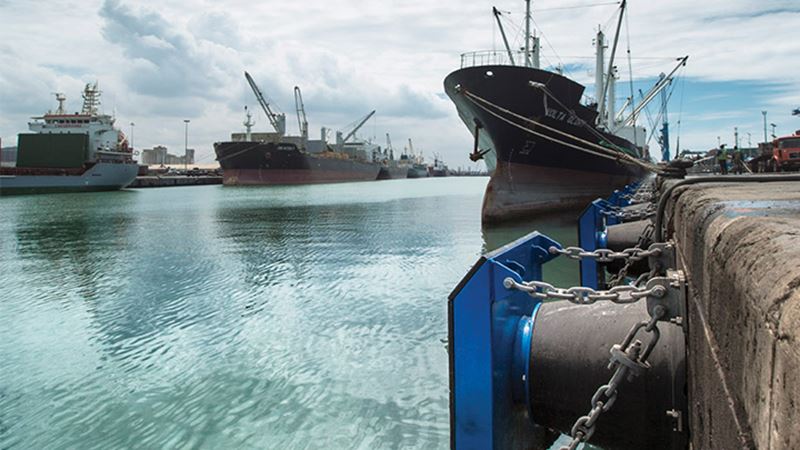
With larger vessels, increased cargo volume, improved safety awareness and tougher environmental regulations, today’s ports face significant challenges. To accommodate regional compliances and the rapidly changing nature of the shipping industry, ports must find ways to upgrade and future-proof their infrastructure, doing so safely, efficiently, cost-effectively and sustainably.
Fender systems are a critical part of the port infrastructure. Fenders are mission-critical equipment, and are essential to the safety and efficiency of port operations, protecting vessels and terminals alike. Taking a whole system approach ensures high-quality fender systems optimize vessel throughput and port operations efficiently and safely over the long-term. That’s because a whole system approach to fenders – one that includes application engineering, detailed design, production and quality control as well as installation, operations and maintenance – will reduce construction costs, downtime and operating expenditure. This is in addition to contributing to more efficient berthing operations by improving turnaround times, while improving overall operational efficiencies and reducing operational safety risks.
Application engineering
A high level of technical expertise and application engineering is required when it comes to the design and selection of fender systems, which must be able to protect modern ports and terminals, a wide range of vessels and high-value cargo.
During application engineering, information such as berthing data, site conditions and environment needs to be collected. These are assessed alongside other design criteria − such as local standards, desired service life, maintenance cost and frequency − to determine a project’s unique requirements.
Once all the functional and operational design parameters are determined, accurate and comprehensive application of berthing energy calculations should be made to engineer the best-fit fender solution.
The kinetic energy of a berthing vessel needs to be absorbed by a suitable fender system. To ensure the fender system absorbs the required amount of energy in actual conditions, fender performance correction factors should be considered. When it comes to fender selection at the application engineering stage, there are two fundamental criteria:
- The energy capacity of the fender under the worst operating conditions must be greater than the abnormal design berthing energy.
- The reaction force exerted by the fender onto a vessel/structure must be less than the vessel’s hull pressure limit and fender mounting structure capacity.
Berthing factors such as angular factor, temperature factor, and velocity factor, need to be considered during the selection of a fender, and data should be backed up with testing documents and published in a catalog. Applying the right performance correction factors is vital to overall fender performance and enhances the lifetime of the fenders, reduces maintenance costs and lowers operational risk.
Best-practice specification
To ensure fenders are fit for purpose, they must be produced in accordance with the specifications of a project. When supplying fenders for a project, a range of application details and fender component information, such as panels and chains, must be specified. Fender specification should be carried out right at the very start of a project to ensure that the right fender system is selected – one that will function as required in its intended environment.
A data-driven approach
Taking a data-driven approach to fender design can improve accuracy, reduce costs and enhance port safety. Combining internal data on fenders and external data from the ports, such as berthing speeds, gives port authorities, terminal operators and consultants a clear view of how to improve the design of marine structures.
Meeting current guidelines
Fender systems should be designed in accordance with PIANC’s 2002, the ASTM F2192 or British Standard Code of Practice for Maritime Structures: BS 6349, and be subject to performance and material verification testing, as well as fatigue/durability tests, where applicable. These tests ensure design criteria are met and that a fender system and its components will perform as intended.
Installation
The installation of fender systems should also be considered early in the design process. This is because the accessibility for maintenance, wear allowances and protective coatings will all affect the design and selection of the final fender system.
Detailed fender system design
Once a fender has been selected, the detailed design of the system must be executed and optimized by the fender supplier. This ensures that when in-situ, it delivers superior performance throughout its lifetime, from enhanced safety, lower lifecycle costs and quicker turnaround times, through to reduced maintenance and repair, better ship stability under mooring and increased sustainability levels. Key considerations in best-practice design are:
- Maximum reaction force
- Fender components including accessories
- Front panel design
- Low-friction facing pads
- Restraining chain design
- Fastening system
- Corrosion protection
- Design checks
- Fender system architecture
Fender production and quality control
If the right fender system is selected during application engineering and correctly designed during detailed engineering, the fender that is procured will need to meet the expectations that have been set. This means all parts of the fender system must be produced according to their relevant manufacturing standards to ensure the fender system performs in its intended environment.
Fender system ensures design criteria are met and that a fender system and its components will perform as intended.
To guarantee the performance and durability of a fender system over a lifetime, there are three crucial factors that must be considered in relation to production.
Quality of materials
Understanding how the material composition impacts the quality and durability of a fender system is critical. If poorly designed or made from low-grade materials, the performance and longevity of the whole fender system will be compromised, including the fender, the front panel, the low-friction pads and accessories. Comprehensive material testing is therefore needed to ensure the accuracy of compounds used throughout the manufacturing process.
Manufacturing process
Building and curing processes have a significant impact on the final performance of rubber fenders and therefore the overall fender system. It is important to determine a manufacturer’s expertise and capabilities in these areas and to understand how the different processes affect fender performance.
Independent quality and performance verification
Fender systems projects involve sizable contracts and budgets - there is too much at stake to allow manufacturers to serve as their own regulators. In order to ensure objective, trustworthy results for marine fenders, performance verification testing must be conducted in an independent laboratory or by an independent company with its own testing equipment, which works independently of the manufacturer. This will remove any uncertainty from the results and enable end-users to have the confidence that the lifecycle and performance of fenders meet specifications, and that the fenders are therefore fit for purpose.
Fender system installation, operations and maintenance
Correct installation of a fender is vitally important to it performing as required. When installation is considered early – as part of a whole system approach to fender design – fender systems can be produced to perform optimally in a specific environment. This increases the lifetime of the fender system, reduces downtime and maintenance and supports safe, continuous operations. Installation and commissioning support should be provided by the fender supplier. This includes installation, training, manuals, oversight and supervision.
Regular inspection reduces overall maintenance requirements. Leading suppliers have the experience and skills to provide support with on-site supervisions, as well as regular fender system inspection and make recommendations on maintenance. This increases a fender’s longevity, reduces operating expenditure and ensures the fender system performs as intended over its full product lifetime.
Sustainability is also an increasingly important consideration. A low-cost fender – made from low-quality materials – will have a shorter lifespan than a high-quality fender. Since rubber is still hard to recycle, the selection and design of rubber fenders can have a significant environmental impact on a port’s sustainability credentials. High-quality products with a longer lifetime significantly reduce replacement and recycling to support sustainability.
To help address the challenges fender systems face in demanding environments, in which fender systems operate, the supplier should offer clients a full range of after-sales services. High-quality after-sales support incorporates repair services, tailored inspection and maintenance programs, access to spare parts, timely technical support, on-site service and even customized training programs that enable ports to invest in their people.
Conclusion
A high level of technical expertise and experience is required to select the most suitable fender system to safeguard berths, vessels and port operations. Taking a whole system approach with the support of a supplier with a proven track record is vital to ensuring that this mission-critical equipment is able to facilitate safe, efficient and sustainable port operations.