More to XploR ™
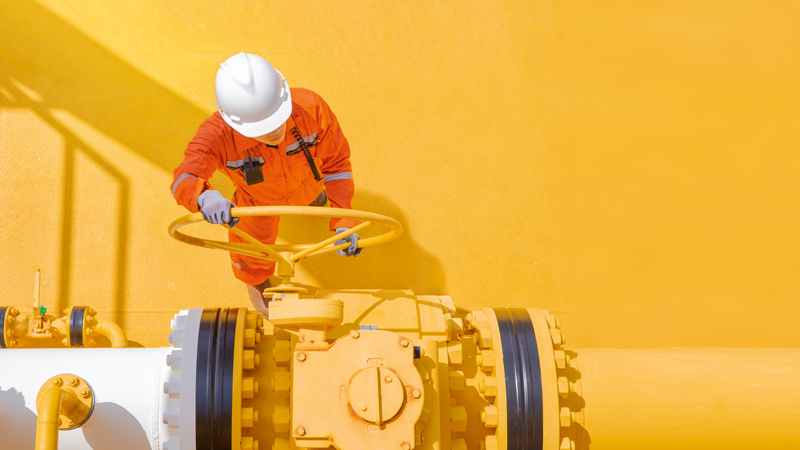
IN SHORT
- As the oil & gas market rebounds faster than expected, increasingly challenging conditions are explored for resources.
- Trelleborg Sealing Solutions introduces two new seals for high pressures and temperatures: XploR™ S Seal and XploR™ FS Seal.
- These seals feature integrated anti-extrusion springs to provide rigidity while remaining flexible, improving performance and making installation quick and easy.
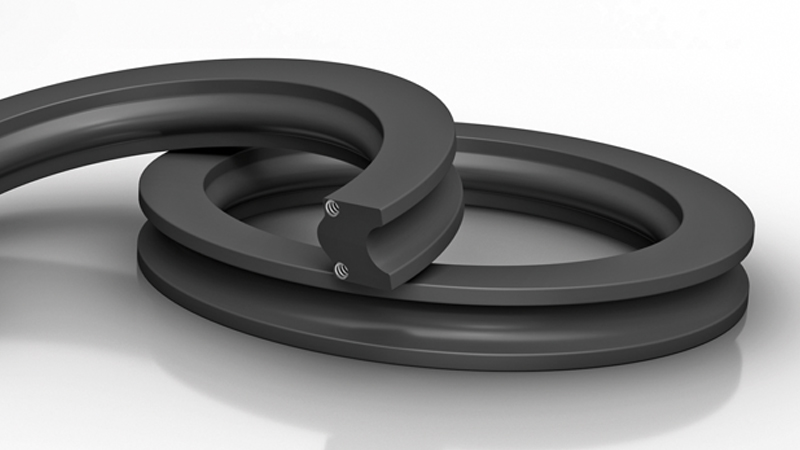
The XploR™ S Seal and XploR™ FS Seal are both primary, bidirectional, static seals optimized for stability in the groove under high pressures and temperatures. They each have specially designed profiles and can be custom engineered to adapt them to different applications, from downhole tools to wellheads and tubing hangers.
The secret behind their strength is the two integrated anti-extrusion springs, which provide a rigid backbone while maintaining flexibility. Hidden beneath the rubber, they provide strong extrusion resistance to the seal while the elastomer element maintains a gas-tight seal when un-pressurized. During operation, the springs work with the pressure to increase the sealing effect. “As system pressure increases, the anti-extrusion springs are forced into the extrusion gap area providing a robust and reliable seal. Coupled with the rubber sealing interface, leak-free operation is possible and allows for significantly reduced emissions,” says Eric.
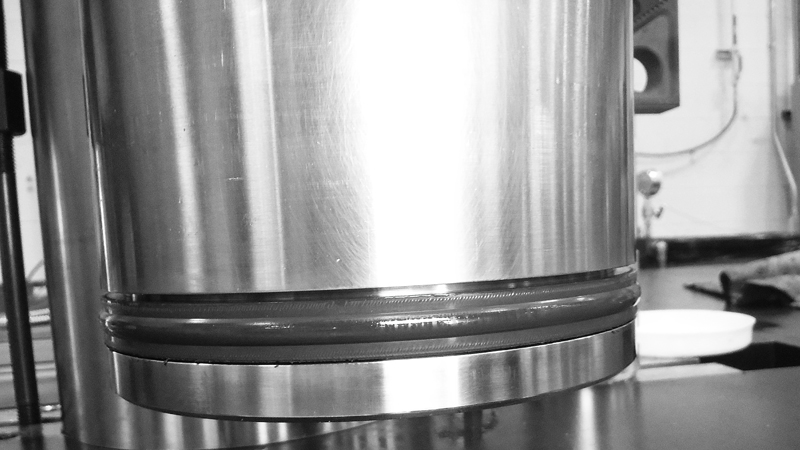
The operating parameters of the seal are mainly decided by the material choice. The XploR™ range is renowned within the Oil & Gas industry and is specified as standard for both products. Resistant to Rapid Gas Decompression (RGD) and aggressive process media, the materials conform to necessary approvals and standards, such as ISO 23936-2 (NORSOK M-710), API-16C, and ISO 10423.
“Compounds behave differently under different conditions, and often to increase performance in one area, another property, such as media compatibility or temperature range, must be compromised on. It takes knowledge and skill to balance these factors and create a material that perfectly fits an application. That’s what we’ve done with the XploR™ materials; matching the compound with the application,” says Eric.
The XploR® range is drawn from a larger portfolio of materials, including the high-specification Isolast® compounds, which are available for use when required.
To provide confidence in the performance of the design and materials, Trelleborg Sealing Solutions undertook testing regimes relevant to oil & gas regulations. The products are validated in accordance with ISO 10423 Annex F conditions at a range of key temperatures. “The validation testing is very difficult, yet Trelleborg Sealing Solutions has one of the largest compliant material portfolios in the industry,” says Eric.
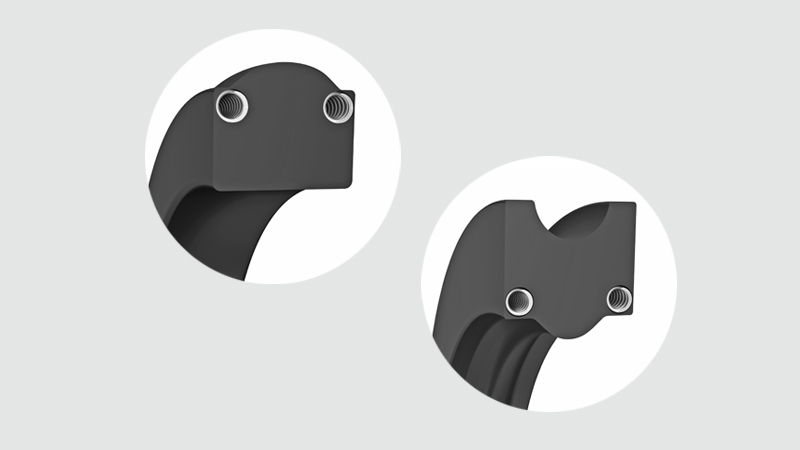
Primary one-piece static seals for Oil & Gas applications. They give bubble-tight sealing at high pressures and temperatures with superior extrusion resistance. Their design manages high hardware tolerances and applications, such as valves and downhole tools where pressure can cause ballooning of hardware.
FEATURES
- High pressures up to 103.4 MPa / 15000 psi
- Temperatures up to -45 °C / +260 °C ; -49 °F / +500 °F depending on material choice
- Replace several components with a single seal
- Compliant with multiple industry standards, such as ISO 29001 Oil & Gas design & manufacturing.
- Compliance to API 6A / ISO, API-16C 10423 Annex F, PSL 3 & 4; Materials compliant to NORSOK M710.
- Material choices to meet any conditions
- Cost-effective
- Robust and flexible with symmetrical cross-section for error-free installation
- Seals effective even with relatively rough surfaces
- Same quality and standard product anywhere in the world
APPLICATIONS: Oil & Gas industry, including Drilling Tools, Downhole Tools, Trees, Wellheads, Valves, Risers & Connectors, Coil Tubing Equipment, and Fracking Equipment. Chemical Processing and Transport.