A ‘No Stop’ Solution
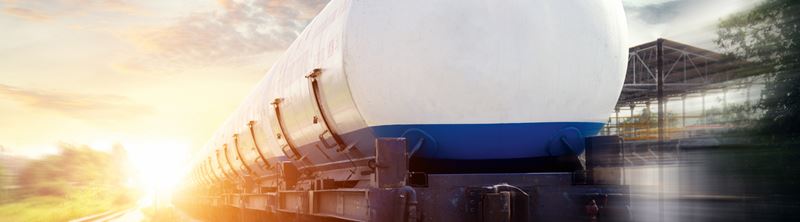
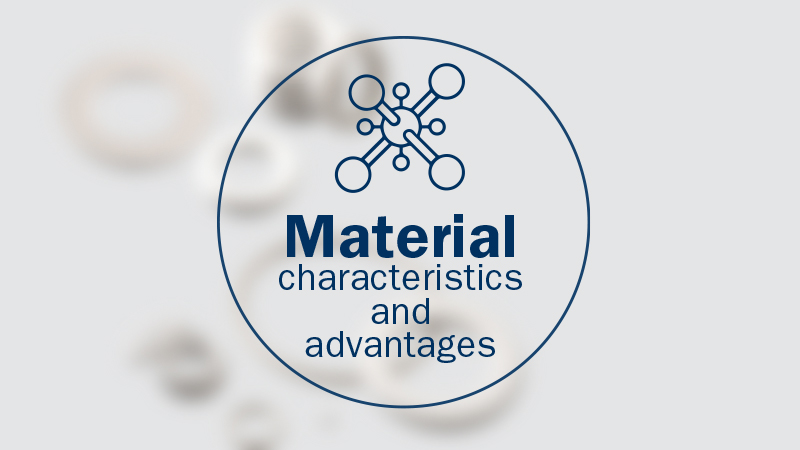
Prior to transportation, chemicals are pumped into and out of tanks, and within the tanks’ valves there are numerous seals. Intrinsically, the type of chemicals transported will potentially cause sealing materials to prematurely deteriorate with some media being extremely destructive. Zero-leakage is mandatory to avoid any pollution and meet strict regulations.
Thijs Menzel, Segment Director, Chemical Transportation, says, “To make transportation as effective and economical as possible for the carrier, the ideal is that the same valve can be used in the tank whatever the media transported. Irrespective of conditions, seals must provide long life so that downtime, maintenance and valve replacement is minimized.
“This avoids rework to swap-out the seals in the valves. Though the seals themselves would be relatively low in value, the labor to bring the tank into the shop and perform maintenance, and the lost up-time during maintenance and while waiting for an inspector to sign off on work done, can be costly. Consequently, fewer seal changes can significantly lower the total cost of ownership for an equipment owner or shipper.
“Sealing materials in the valve in the tank must, therefore, be resistant to the maximum number of chemicals that could potentially be transported in the tanks. Add to this challenge the environmental conditions that freight may be exposed to; traveling across deserts in extreme heat or over ice fields at low temperatures, for instance. This makes universal sealing across the full range of chemicals potentially transported, an almost unsurmountable task.”
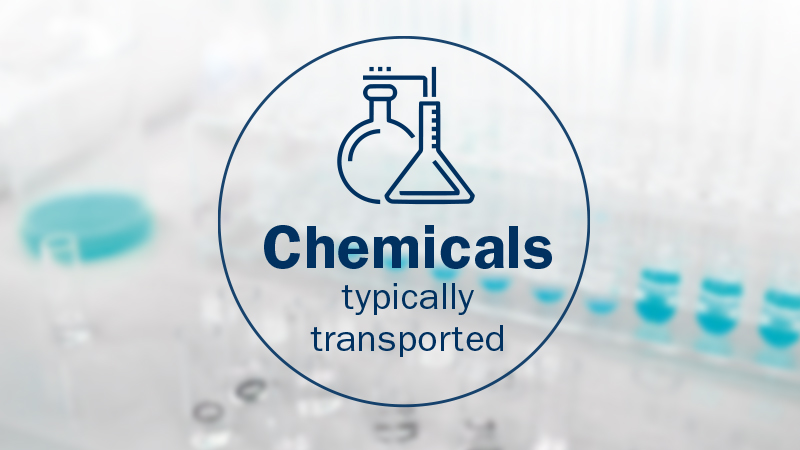
These requirements mean that for transportation of certain commodities, the only possible type of sealing material that can be used is Perfluoroelastomer (FFKM), which exhibits the sealing qualities of an elastomer combined with the chemical resistance of a Polytetrafluoroethylene (PTFE). However, not all FFKMs are made equally. Special properties are needed to stand up to the harshest of chemicals likely to be transported.
Thijs mentions a trend toward transportation of harsher media, not just as a single medium, but as cocktails of chemicals. Again, this means that a sealing material that is as universally compatible as possible is a paramount requirement for owners and shippers.
“A particular example is MTBE, an additive for diesel fuel or ethanol that is a denaturant, which is extremely destructive to sealing materials,” says Thijs. “MTBE prevents ethanol from being consumed as an alcohol, allowing it to be de-taxed by the US Government.
"Also, under the Sulphur 2020 initiative, higher-grade diesel is replacing previously prevalent bunker fuel, and this has MTBE in it. Both of these factors are increasing the number of shipments of ethanol and diesel with added MTBE.”
Testing proves performance
Isolast® J9503 and Isolast® J9567 are existing advanced proprietary FFKM compounds in the Trelleborg Sealing Solutions material portfolio. Based on experience in other segments and with their outstanding media compatibility and sealing performance, we believed that these materials could effectively endure the rigorous conditions faced in chemical transportation over the broadest range of media.
To prove this, Trelleborg Sealing Solutions subjected Isolast® J9503 and Isolast® J9567, as well as three competitive FFKM materials, to an extensive testing program involving the sixteen chemicals most transported.
Acetone – Organic compound that is a commonly used as a solvent
Ammonium Hydroxide – Solution of ammonia in water that is used as a cleanser and in manufacturing of plastics, rubber, fertilizer and textiles
Butyraldehyde – An organic compound that is used in production of plasticizers
Diethyl Ether – An ether used as an inhalation anesthetic, non-polar solvent and refrigerant
Ethanol – A simple alcohol used in a variety of products and processes
Ethyl Acetate – Acetate used in glues, nail polish removers and in the decaffeination process of tea and coffee
Ethylenediamine* – Organic compound commonly used as a building block in chemical synthesis
Ethylene Glycol – Organic compound used as a raw material in the manufacture of polyester fibers and antifreeze
Glacial Acetic Acid* – A water-free acetic acid and a precursor to polyvinyl acetate and cellulose acetate
Mobil Jet 11 – High performance aircraft-type gas turbine lubricant formulated with a combination of a highly stable synthetic base fluid and a unique chemical additive package
Methyl tert-butyl ether (MTBE)* – Organic compound used as a blending component to oxygenate and raise the octane of gasoline
Nitric Acid – Mineral acid commonly used as a strong oxidizing agent
Sodium Hydroxide – A caustic base and alkali that is used in many industries
Sulfuric Acid – Mineral acid commonly used in manufacturing and processing
Toluene – Aromatic hydrocarbon used as a solvent in various products, such as paint thinner or contact cement
Urea – An organic compound that is an important material in chemicals
* These chemicals tend to be the most destructive to sealing materials.
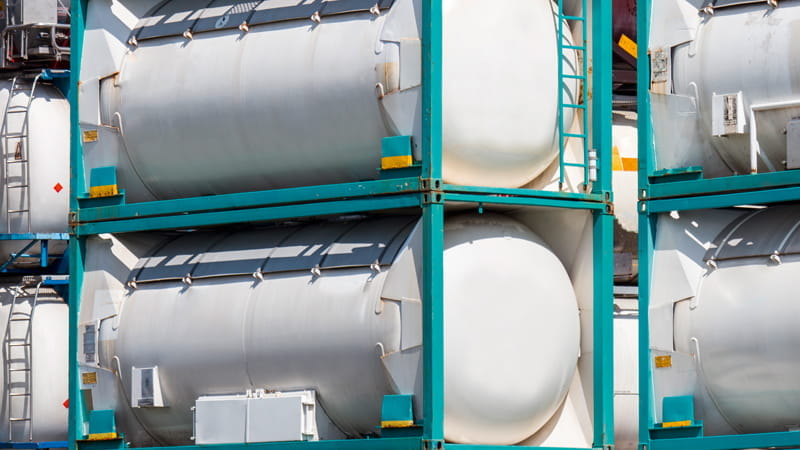
Trelleborg Sealing Solutions testing focused on key criteria effecting sealing performance and the life of the seal, the most important being volume change. The lower this is,
the better the long-term sealing performance.
Superior performance
In all media, both Isolast® J9503 and Isolast® J9567 hada volume change of less than 10%; a level that is deemed to have at its maximum, only a moderate effect on sealing performance. In 12 out of 16 media for both Isolast® J9503 and Isolast® J9567, the volume change was below 5%; a level that is deemed to have little or minor effect on sealing performance.
The Isolast® compounds were back-to-back tested against three competitive products. Two of these competitive compounds displayed a volume change in one of the media above 20%, meaning the material would not be recommended for use in that media.
All testing was conducted against ISO 1817 standards. Hardness and volume change were monitored for an extended period, of 2000 hrs. This testing regime far exceeded the standard requirement, which monitors physical changes in the material over a limited seven-day period.
Significantly better in destructive media
Both Isolast® J9503 and Isolast® J9567 performed exceptionally well in the media that is most destructive to seals–Ethylenediamine and Glacial Acetic Acid. In fact, Isolast® J9503 exhibited the best volume change performance of all materials tested in both chemicals. Two of the competitive materials failed in either Ethylenediamine or Glacial Acetic Acid, rendering both materials incapable of delivering fully universal compatibility with all chemicals potentially transported