Engineered to be One
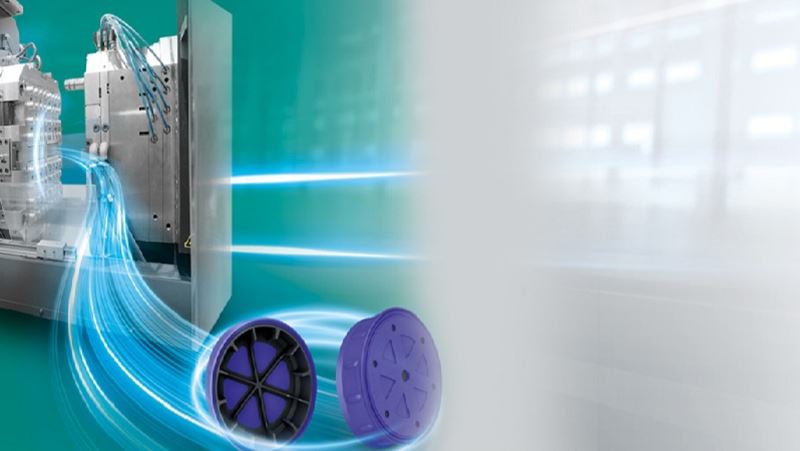
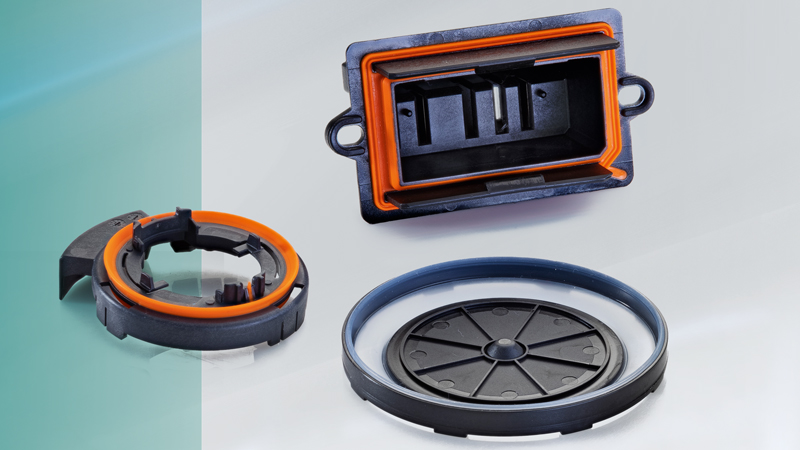
A multicomponent part may provide the perfect solution, as one product essentially provides the groove and the seal. By strongly bonding multiple materials together, components can take advantage of different material properties and combine functions into a single, integrated part — at any scale.
Size matters
Take for example a microinjection pump in an automated dosing system; a safety-critical device designed to deliver minute quantities of life-saving medication. These replace the need for a patient to administer a drug at the correct timings and quantities, giving peace of mind, both to the patient and their carers. The entire pump is not much larger than a fingernail and the diameters of the seals are the size of a pinhead.
Friction would mean that the pump could stutter, providing too much or too little of the drug, and lubrication is not an option due to potential interactions with the medicine. On top of this, the pumps need to be delivered in large quantities, to a cleanroom specification, and inexpensively, as they are classified as ‘single-use’ devices to avoid cross-contamination.
Trelleborg Sealing Solutions engineers responded to the challenge with a two-component, medical-grade Liquid Silicone Rubber (LSR) solution. “With a product this small,
installing multiple seals is nearly impossible. Only a 2K solution could meet all of these requirements,” says Carolin Grandt, Commercial Director Manufacturing at Trelleborg Sealing Solutions.
“In Stein-am-Rhien, we have automated production within ISO-class cleanrooms, providing consistent quality at high quantities, as required by the application.” The pump cylinder is fully lined with silicone material, to both seal and prevent stick-slip at the same time. The LSR process injects the two materials simultaneously using Swiss-precision, custom-made tooling that bonds the materials in a single step. “Without this technology, it would not be possible to produce this micro-sized device that is now available and improving peoples’ lives,” says Carolin.
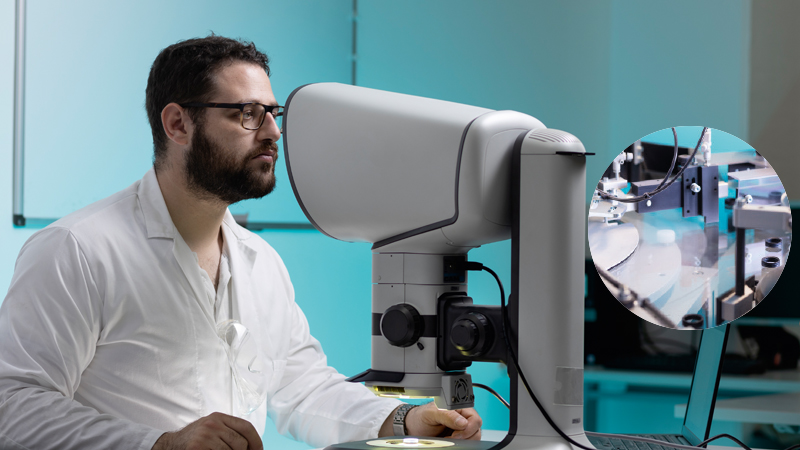
But size is not the only benefit to one-piece solutions. Many applications do not require just a single seal, but a series of components to work in tandem to operate effectively, each taking time to install. “Planned and unplanned maintenance are often cited amongst the main causes of inefficiencies when analyzing the cost of downtime,” says Carolin. “When manually installed, simple errors such as incorrect seal fitting, will cost time and money in repositioning and rectifying the mistake.”
Trelleborg Sealing Solutions encountered such an application with an Electronic Control Unit. Multiple seals were required and each needed to be seated perfectly within the housing.
Several other components, serving different functions, also needed separate installation in the same area. After detailed analysis, including functional testing and Finite Element Analysis (FEA), a new solution was developed.
“We replaced it all with a single integrated component: a combination of plastic and LSR, precision molded into a single part, with four metal inserts in each of the corners,” says Carolin. Though challenging to design and produce in the earlier stages, the time savings are apparent. “With high specification LSR on the inner sealing lip, the metal inserts providing the necessary strength on the housing and a custom plastic connector to hold them in place, assembly was reduced to a single, fool-proof step,” explains Carolin.
Multicomponent Development Center
When a new multicomponent plastic-to-elastomer solution is being developed, Trelleborg Sealing Solutions calls on its dedicated Multicomponent Development Center. This stateof- the art facility is responsible for developing, testing and validating solutions in quasi-series production conditions. The center is set up for a full suite of operations, including bond strength testing for a range of material combinations, and process parameter optimization, both of which are crucial to validate and optimize multicomponent products. “We have invested in rapid prototyping capabilities to give our customers a fast and effective turnaround time on manufacturing feasibility and testing,” says Neal Borg, Product Manager for Multicomponent Solutions at Trelleborg Sealing Solutions.
Trelleborg Sealing Solutions uses its global network of manufacturing, design and logistics centers to support its customers’ businesses, wherever it is in the world. This means speaking their language and understanding their market and requirements. “Being global, the customer can tap into our pool of expertise. Our engineers will use the latest technologies and world-class production facilities to ensure the best solution for your specific application,” says Neal.
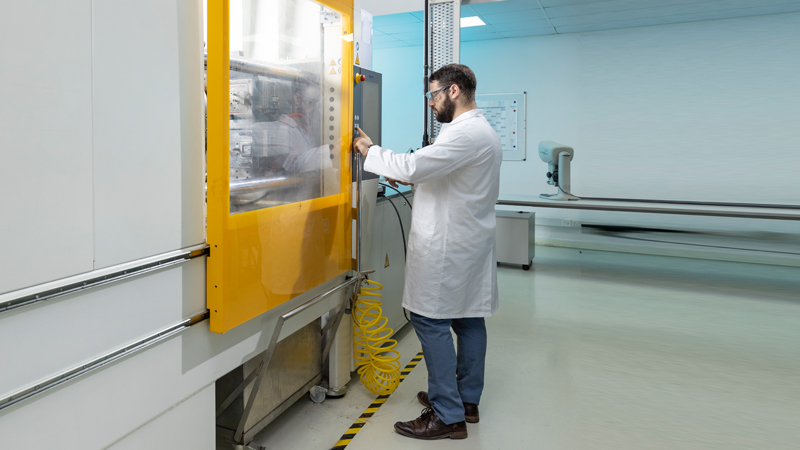
Competencies and capabilities
Multicomponent sealing solutions are suited to various industry requirements and lend themselves to an extensive list of applications. Two of the most common application requirements are reducing the number of components needed and making installation easier and less time consuming. “Product and application complexity require engineering expertise as well as state-of-the-art equipment. Our engineers are at your service to work with you to achieve the best product performance and most cost-effective sealing solution,” says Neal.
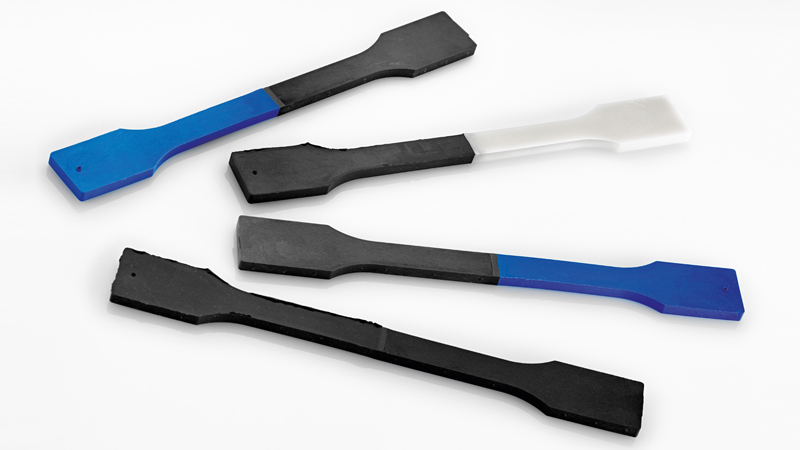
We offer one of the most complete material portfolios on the market that is engineered to withstand the most demanding conditions. We have developed a range of techniques and processes to achieve strong bonds between these and with other compounds and metal, ensuring there are no leak paths.
Trelleborg Sealing Solutions is the market-leading provider of plastic to elastomer solutions. The state-of the-art technology, expertise and toolmaking required is provided by very few companies on the market.
Unique multicomponent material combinations:
- Plastic to Thermosetting Elastomer (Rubber)
- Plastic to Liquid Silicone Rubber
- Plastic to Thermoplastic Elastomer
The type of materials chosen depends greatly on the application. Our engineers work with you to analyze many factors, such as media encountered, temperature range and mating surfaces, to fully understand the sealing issues and develop the best solution.
There is a vast range of polymers available for multicomponent solutions, including thermoplastic elastomers.