Escape slide
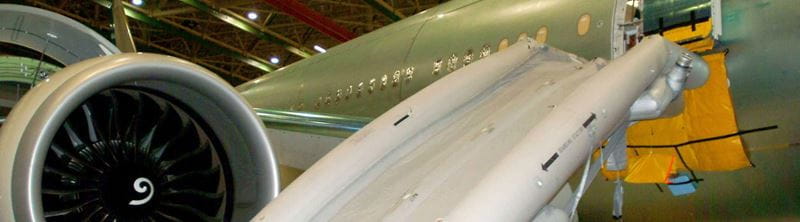
Date: 31.08.13
Airliner evacuation slides remain copmliant with Trelleborg´s coated fabrics
Over the last 50-plus years, the technology used within the production of aeroplanes has become much more sophisticated and innovative as a result of stricter legislation, which has been refined over the years following analysis of transportation accidents, to ensure the safest and most robust aeroplanes.
With the expertise to respond to these developments without difficulty, particularly in the manufacture of emergency escape slides, is Trelleborg Coated Systems’ Engineered Fabrics business - a leading global supplier of unique customer solutions for polymer-coated fabrics deployed in several industrial applications, including the aeronautical industry.
Johan Frithiof, Commercial Director within the Engineered Fabrics business of Trelleborg, commented: “The design requirements of airliner evacuation slides have become much more stringent in the last 50 years. In the 1960’s they had to be deployed in 25 seconds in non-extreme weather, meaning no wind and only medium range temperatures. Now, the FAA states that slides must deploy in just six seconds, in heat ranging from -65 to 160 degrees Fahrenheit and winds of up to 25 knots (28.7mph).”
There are three main categories of requirements used for evacuation system design and operation - the FAA’s Technical Standard Order (TSO) C69 which defines mostly performance criteria, FAR and JAR 25 which covers airworthiness standards and FAR 121 and JAR OPS 1 which defines operating requirements.
Specifically, the FAA’s TSO-C69 has seen a number of additions over the years, following full testing and analysis as well as safety requirements from the National Transport Safety Board (NTSB), with its original issue on 15th August 1961. Since then, TSO-C69a was issued on the 3rd June 1983 to include radiant heat testing requirements in case of a fire, increased material flammability and revised strength requirements of the slide’s material.
Similarly, the evacuation rate was increased from 30 to 60 evacuees per minute, inflation time decreased from 25 to 10 seconds, the requirement for side guards and self illuminated slides, as well as deployment capabilities in 25 knot winds. At least five deployment and erection tests must be demonstrated without failure to prove its performance.
On the 17th August, 1988, TSO-C69b was launched which saw the requirement for the off-wing slide ramp floor fabric to be puncture proof. Inflation times were also decreased from 10 seconds to 6 seconds. An additional wing-to-ground slide now requires the device to automatically erect from 15 seconds to 10 seconds after actuation of the inflation control.
Finally, on the 18th August, 1999, the latest guidelines were introduced under TSO-C69c, which included the increase of evacuation rate from 60 to 70 passengers per minute, per lane, the addition of a beam strength test to accommodate three evacuees sliding down bunched together and the requirement of actual testing in the dark of night with naive subjects to test the lighting system efficiency. In addition, radiant heat testing requirements meant that the pressure holding materials must meet the 90 second minimum-time-to-failure requirement and the 180 second average-time-to-failure.
Frithiof continued: “Over the years, our expert teams of chemists and engineers have refined the characteristics of our coated fabrics to ensure consistent high performance and compliancy, by withstanding much higher temperatures and harsher weather, while meeting weight reduction needs and making downstream process improvements.
“At Trelleborg, we put all of our fabrics through physical, chemical and textile tests to ensure that elements such as tear strength, flame resistance and aging, for example, are all carefully considered and measured to ensure compliant solutions every time.
“The nature of emergency products means that you hope they never have to actually be used. But, when they are needed it is imperative that they are in full working order.”
With the expertise to respond to these developments without difficulty, particularly in the manufacture of emergency escape slides, is Trelleborg Coated Systems’ Engineered Fabrics business - a leading global supplier of unique customer solutions for polymer-coated fabrics deployed in several industrial applications, including the aeronautical industry.
Johan Frithiof, Commercial Director within the Engineered Fabrics business of Trelleborg, commented: “The design requirements of airliner evacuation slides have become much more stringent in the last 50 years. In the 1960’s they had to be deployed in 25 seconds in non-extreme weather, meaning no wind and only medium range temperatures. Now, the FAA states that slides must deploy in just six seconds, in heat ranging from -65 to 160 degrees Fahrenheit and winds of up to 25 knots (28.7mph).”
There are three main categories of requirements used for evacuation system design and operation - the FAA’s Technical Standard Order (TSO) C69 which defines mostly performance criteria, FAR and JAR 25 which covers airworthiness standards and FAR 121 and JAR OPS 1 which defines operating requirements.
Specifically, the FAA’s TSO-C69 has seen a number of additions over the years, following full testing and analysis as well as safety requirements from the National Transport Safety Board (NTSB), with its original issue on 15th August 1961. Since then, TSO-C69a was issued on the 3rd June 1983 to include radiant heat testing requirements in case of a fire, increased material flammability and revised strength requirements of the slide’s material.
Similarly, the evacuation rate was increased from 30 to 60 evacuees per minute, inflation time decreased from 25 to 10 seconds, the requirement for side guards and self illuminated slides, as well as deployment capabilities in 25 knot winds. At least five deployment and erection tests must be demonstrated without failure to prove its performance.
On the 17th August, 1988, TSO-C69b was launched which saw the requirement for the off-wing slide ramp floor fabric to be puncture proof. Inflation times were also decreased from 10 seconds to 6 seconds. An additional wing-to-ground slide now requires the device to automatically erect from 15 seconds to 10 seconds after actuation of the inflation control.
Finally, on the 18th August, 1999, the latest guidelines were introduced under TSO-C69c, which included the increase of evacuation rate from 60 to 70 passengers per minute, per lane, the addition of a beam strength test to accommodate three evacuees sliding down bunched together and the requirement of actual testing in the dark of night with naive subjects to test the lighting system efficiency. In addition, radiant heat testing requirements meant that the pressure holding materials must meet the 90 second minimum-time-to-failure requirement and the 180 second average-time-to-failure.
Frithiof continued: “Over the years, our expert teams of chemists and engineers have refined the characteristics of our coated fabrics to ensure consistent high performance and compliancy, by withstanding much higher temperatures and harsher weather, while meeting weight reduction needs and making downstream process improvements.
“At Trelleborg, we put all of our fabrics through physical, chemical and textile tests to ensure that elements such as tear strength, flame resistance and aging, for example, are all carefully considered and measured to ensure compliant solutions every time.
“The nature of emergency products means that you hope they never have to actually be used. But, when they are needed it is imperative that they are in full working order.”
Trelleborg is one of the leading suppliers of urethane coated material used in the fabrication of aircraft evacuation slides, with over 100 years of in-house testing expertise. For additional information regarding these products, please visit our web site at Engineered-fabrics.