Prototype tool machining with TC760X
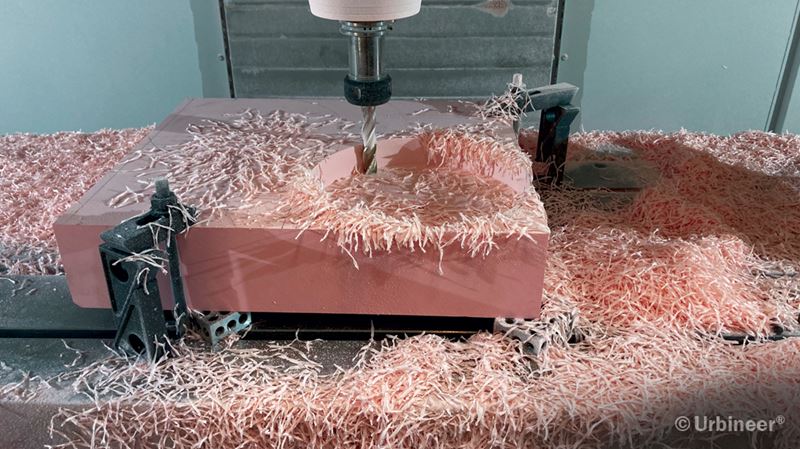
Background
Urbineer® design, engineer and manufacture composite prototype and technical demonstrator parts for the aerospace industry, with expertise in advanced lightweight composite airframes and structures. Finding the right tooling board material is vital for this industry as absolute precision and high performance is key.
Problem
Urbineer® needed a tooling board that offered a higher service temperature and an improved machining environment, whilst maintaining the toughness and durability required for manufacturing precision prototypes. Prototyping requires moving between metal and epoxy boards on the milling machine, creating a large amount of dust that requires extensive extraction and a lengthy clean-up process, taking time to complete. “We needed a solution that offered toughness, durability and stability, allowing us to fabricate high tolerance parts and multipiece tools that not only hold their tolerances but also give the desired finish.” Stuart Marshall Co-founder and CEO of Urbineer®.
Solution
While machining with different tools, Urbineer® found that the TC760X board would slice the material resulting in flakes instead of creating the large amounts of dust that typical epoxy boards produce, even during aggressive roughing passes on the CNC milling machine. This made for a much cleaner machining environment and reduced clean-up time.
By using indexable inserts on the machine cutter, Urbineer® discovered TC760X did not chip at the edges and the roughing passes could be accomplished efficiently, reducing the time on the mill with limited wear to the cutters.
“I have used Trelleborg tooling boards for many years and was excited about the advantages that TC760X offered. There was no learning curve required and the dust free machining environment and surface finish that we were able to achieve will make us a long-term user.” Stuart Marshall Co-founder and CEO of Urbineer®.
Typically, epoxy tooling boards require several hours of manual sanding to achieve a high-quality finish, with the risk of potentially changing the surface profile tolerance by hand sanding. Using TC760X, Urbineer® is able to produce a machined finish tool that requires minimal post-mill sanding, ensuring the surface profile remains unchanged.
An additional benefit of using TC760X was the machined finish achieved with reduced mill passes; the tool only required a few coats of sealer compared to the usual 8 or 9 to achieve a high gloss finish. Tools could then be released to use for direct to part manufacturing, speeding up the overall production time.
The high Glass Transition Temperature (Tg) of TC760X allows Urbineer® to direct cut tooling and not be limited to prepreg part materials with low initial curing capabilities. The high Tg of +140 OC (Tg is the temperature at which the material transitions from its glass state to a rubbery state) means parts can be cured at typical aerospace temperatures, without tool degradation, providing a faster curing time.
“We fabricate high tolerance parts from tooling and TC760X has the durability and toughness to make multipiece tools that not only hold the tolerances but the desired finish directly on the mill. The toughness and durability of the TC760X material enables us to create the sharp edges needed to match tool sections together.” Stuart Marshall Co-founder and CEO of Urbineer®.
“I appreciate when companies like Trelleborg keep developing products that increase the quality and performance that we are able to offer our customers”. Stuart Marshall Co-founder and CEO of Urbineer®.