Whitepapers

Formulated for an Era of New Challenges
When specifying a high-performance material for your medical device application, temperature, environment, compatibility, hardness, compression, and certification considerations quickly build stringent material requirements. Expert suppliers consult with Original Equipment Manufacturers to think creatively, support product development and collaborate to find solutions that will deliver necessary results.

Choose the Right Rubber Material & Process for Your Medical Parts
When it comes to selecting the right rubber material for your medical device, understanding your application, the physical and mechanical properties of your material options and the interaction with mating components will go a long way.

Optimizing the Manufacturing of Custom Rubber Components
In this whitepaper, we’ll equip you with a better understanding of the key elements of rubber component design and manufacturing — from material selection and design, to prototyping and production mold technology.

Medical Device Design for Plastic Injection Molding
This whitepaper explains how mold components affect design and the overall injection molding process, how plastic material selection affects the molding process, and common defects and how to avoid them, helping to ensure that your medical device design adheres to good DfM practices from the initial stages.

Introducing APIs to Silicone and Controlling Elution Rates
This whitepaper reviews the methods for introducing an active pharmaceutical ingredient to raw silicone and explores a new means of controlling long-term elution rates. The paper also takes a closer look at each of these methods and presents test results proving the effectiveness of each.
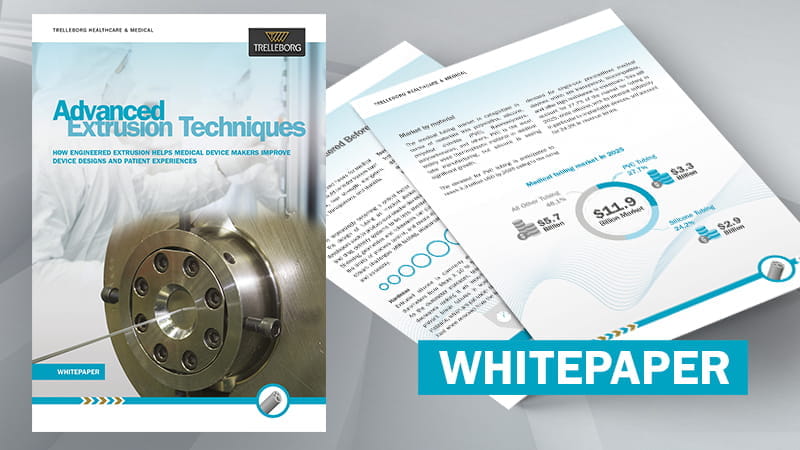
Advanced Extrusion Techniques
Rapid growth in the medical devices industry and changing patient expectations are leading to significant innovation in hosing and tubing. This whitepaper introduces the key factors to be considered in the specification of these extrusions, outlines the material options (focusing on silicone extrusion technologies), and highlights applications with real-life examples from our customers.
Download the whitepaper
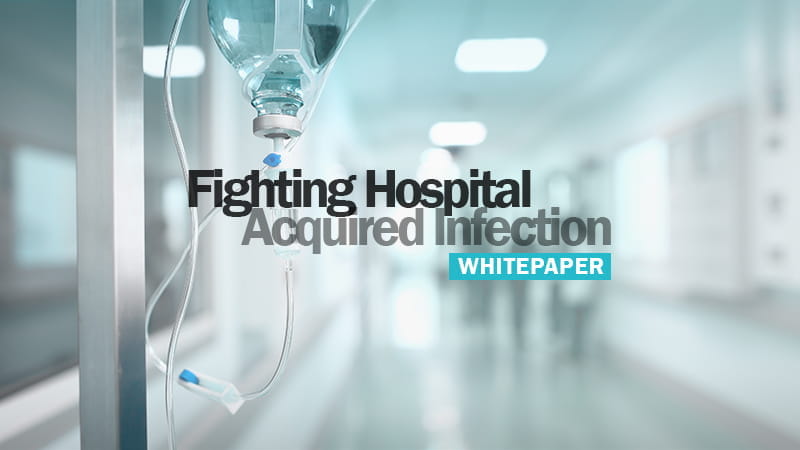
Fighting Hospital Acquired Infection
Hospital-acquired infections have been decreasing over time, however they still remain a threat to patient safety. Our silicone tubing experts have tested a variety of techniques aimed at reducing bacterial colonization. This whitepaper outlines these techniques and presents test results proving the effectiveness of the immersion impregnation method in combining an API with silicone tubing to prevent catheter-associated infections.
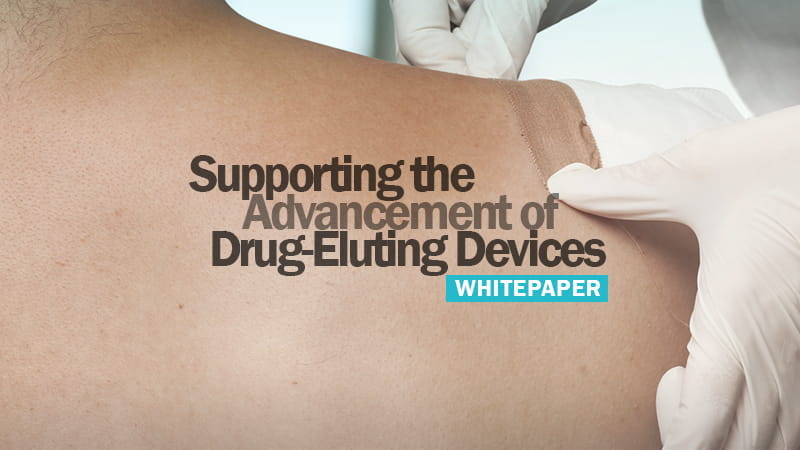
Supporting the Advancement of Drug-Eluting Devices
Our silicone and medical device experts have tested a variety of methods for adding the Active Pharmaceutical Ingredient (API) to the silicone component. This whitepaper compares the methods and presents test results proving the effectiveness of the immersion-impregnation method, which potentially opens drug-eluting devices to delivery of a wider range of API.
Technical Articles
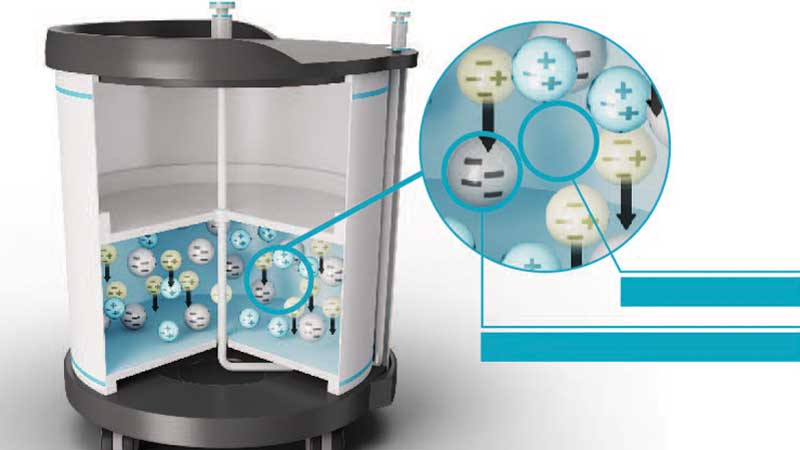
Providing Biopharmaceutical Manufacturers with Cutting-Edge Material and Assembly Solutions
Article originally published in BioProcess International
Trelleborg experts leverage a reinforced polypropylene (PP) composite material´to make thin, light chromatography columns, using significantly less material than is needed for traditional options.
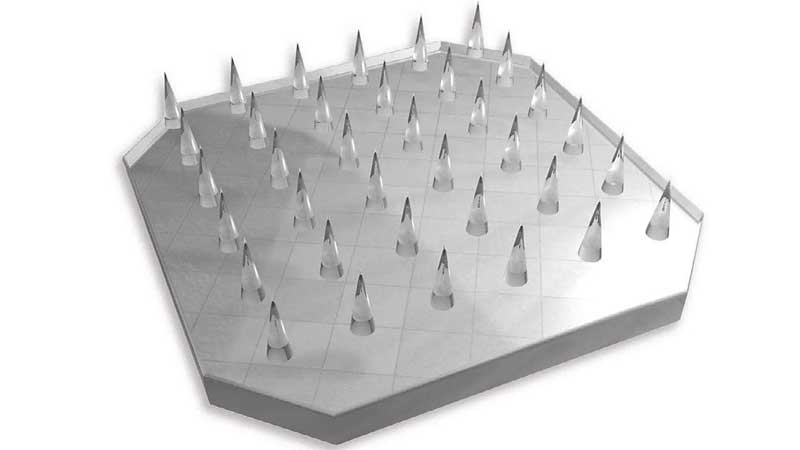
Introducing drugs to silicone and controlling elution rates
Originally issued in Annual Guide – Pharmaceutical Post, December 2022, https://thepharmaceuticalpost.com
Implantable drug delivery systems have the potential to address some of the biggest challenges patients face today. Through continued development of these technologies, many patients living with chronic conditions can realize significant improvement in their overall quality of life.
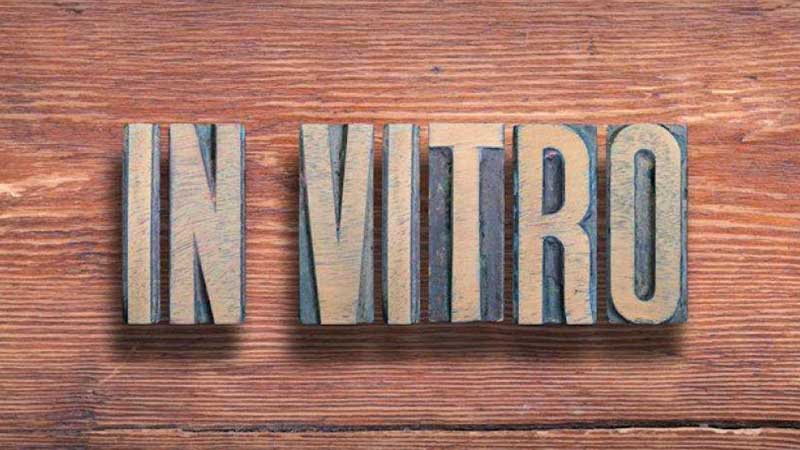
Silicone Tech Advances are Key for In Vitro Device Manufacturers
Today, few industries are as innovative or technologically minded as medical devices, especially when it comes to in vitro diagnostics. In a market that is rapidly growing and changing, in vitro device manufacturers need to meet a key emerging demand for home testing and more rapid lab analysis.
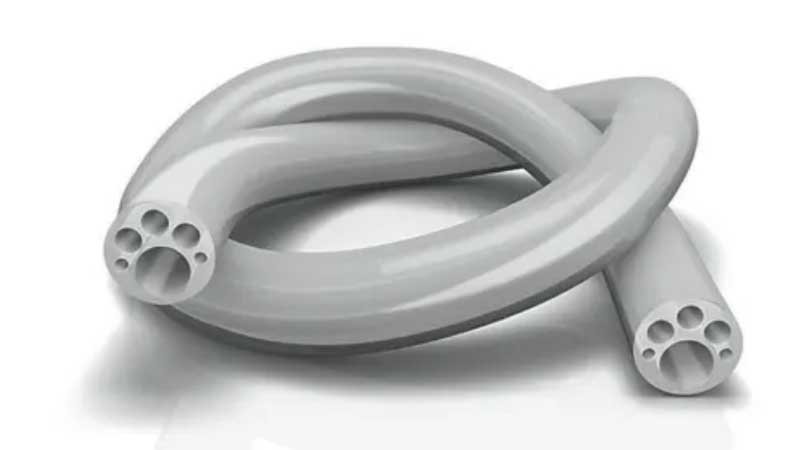
How these Engineered Extrusion Trends can improve Device Design and Patient Experience
Hoses and tubes are extensively used within the healthcare and medical industry in a variety of applications, from wound drains and catheters to drug delivery and feeding tubes. Technology has moved far beyond the production of single, hollow tubes to multilumen extrusions that can incorporate stops, bumps, and varying thicknesses in a single design.

Device Development Excels in Rapid Development Centers
Design and material choices can have a long-term impact on manufacturing costs and effieciencies for medical device manufacturers. When they work together with experienced component manufacturers from the start of a project, they can save time, reduce costs, and produce premium quality products, while keeping an eye on the goal of a smooth transition to serial production.
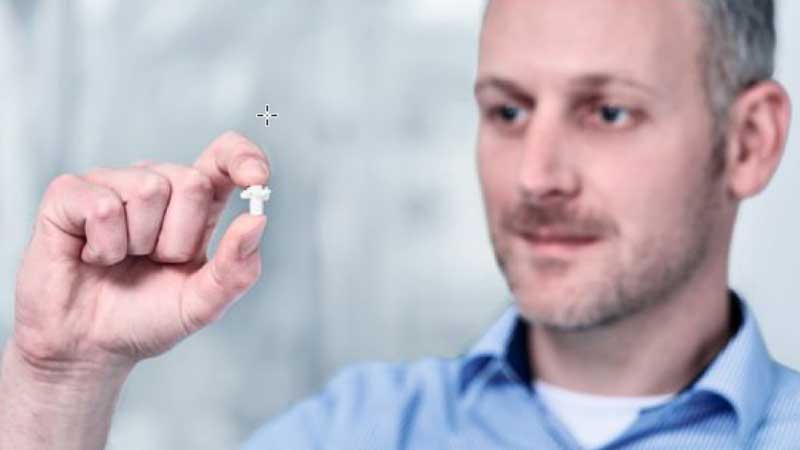
Precisely Pumped Dosages
Handy medical devices make life easier for people with chronic conditions, and automated dosing systems are gradually replacing regular injections of essential medication. Trelleborg cooperated with WACKER to develop a microinjection pump, the very heart of such devices.
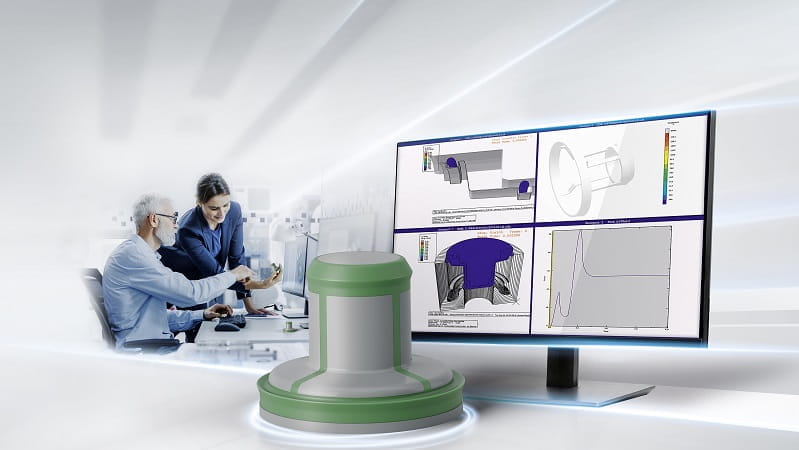
Q&A: Reducing the cost of long-term manufacturing
Medical Plastic News spoke with Chris Tellers, Rapid Development Center director, Trelleborg Healthcare & Medical to learn out about the company's recently
launched Rapid Development Center in Delano, Minnesota
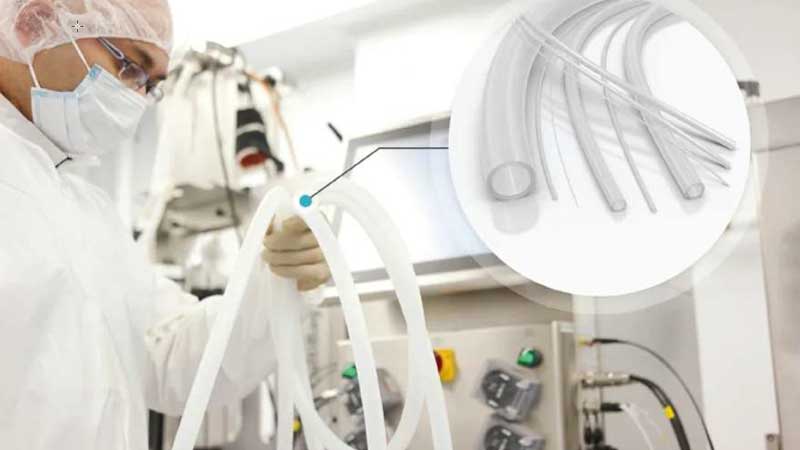
Single-Use Systems: The Future of Bio pharmaceutical Processing
Single-Use systems represent the future in biopharmaceutical processing of therapeutic drugs with significant advantages over traditional reusable stainless-steel systems and partly disposable systems.
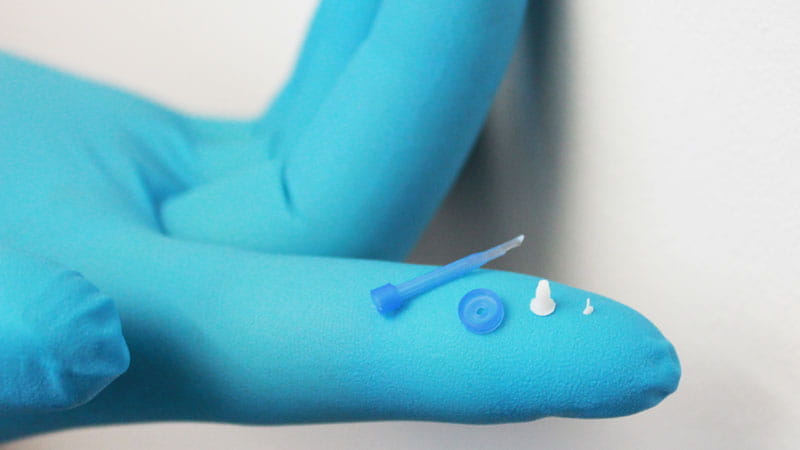
Demand Drives Excellence in Micromolding
Advancements and miniaturization in the medical device industry have improved healthcare around the globe.
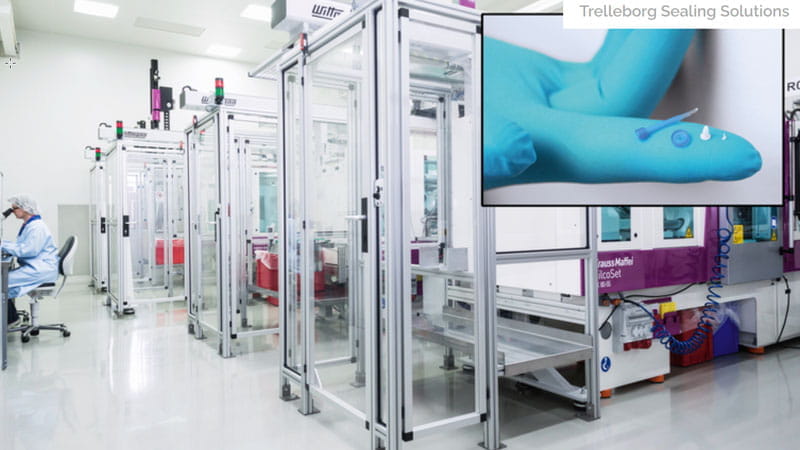
A Mighty, Small Idea
Today’s medical device manufacturers operate in a challenging landscape. Stricter regulations and the need for biocompatibility are making development and manufacturing more demanding. Add to that user requirements for devices that suit their lifestyle choices, such as wearable products and home monitoring solutions, and you can understand why Trelleborg Sealing Solutions engineers are looking for novel component options.
First appeared in Machine Design
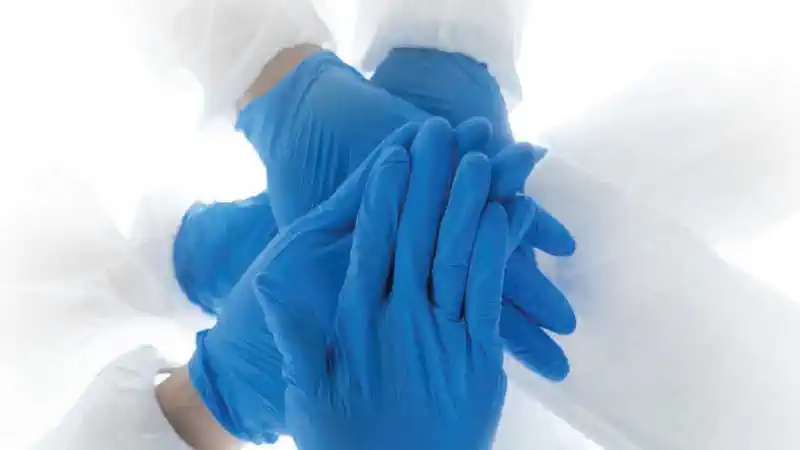
Onward and upward for SUS in bioprocessing
Addressing challenges in single-use system market requires collaboration
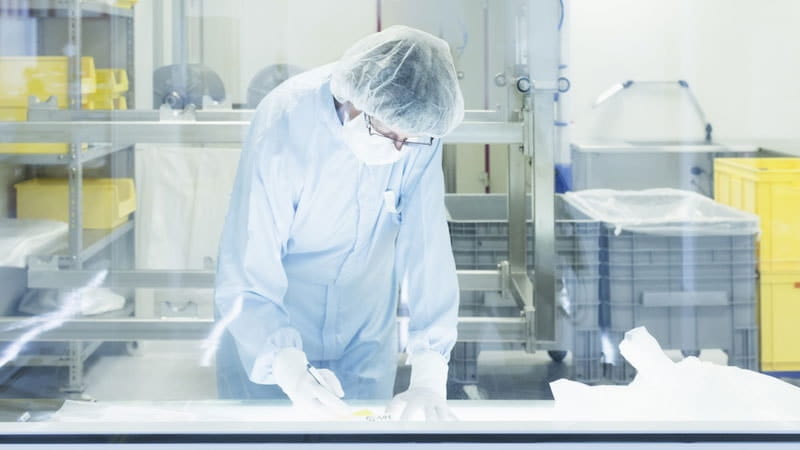
When one is better than many
By Ursula Nollenberger; Trelleborg Sealing Solutions
As medical devices become ever more sophisticated and smaller in size, the challenge for the component manufacturer is how to fit multiple functions into a limited space. Multi-component LSR technology offers a solution to this, that in addition, provides designers with the latitude and flexibility to enhance their applications.
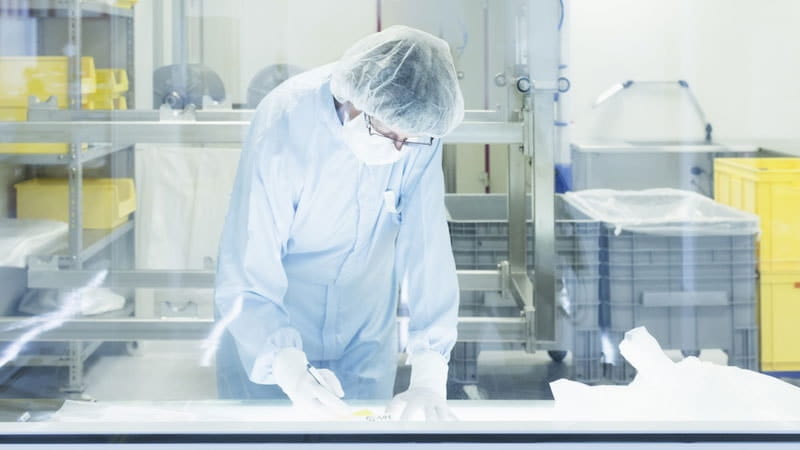
Wenn Einheit besser als Vielzahl ist
By Ursula Nollenberger; Trelleborg Sealing Solutions
Silikon ist ein ideales Material für medizinische Geräte und Systeme. Das Elastomer ist nicht nur inert, biostabil und biokompatibel bei zugleich vorteilhaften physikalischen und haptischen Eigenschaften, es ist darüber hinaus auch auf vielfältige Weise verarbeitbar.
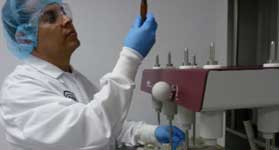
Understanding Key Processes for Mixing API's with Silicone
By Anrew Gaillard, Healthcare & Medical Segment Manager, Trelleborg Sealing Solutions.
The pros and cons of drug delivery and device enhancement.
With its stability and biocompatible properties, silicone is leading the way to a new generation of drug delivery products and enhanced medical devices that will profoundly improve patient care.
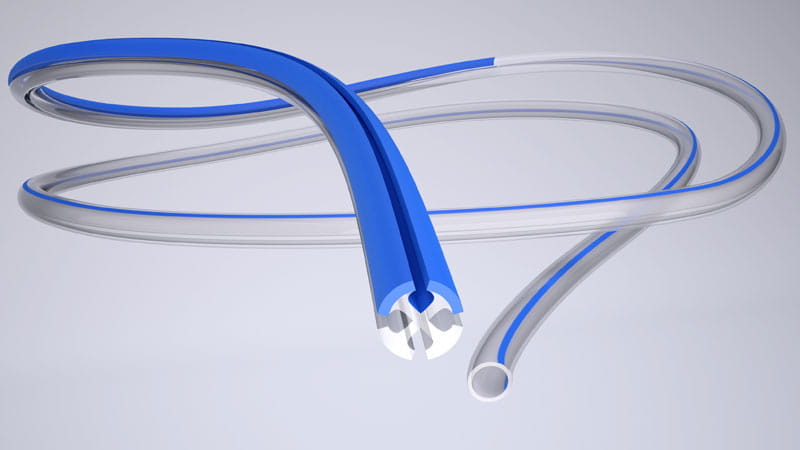
Reducing Risk with Geometric Transition Extrusion
By Dan Sanchez, Product Manager at Trelleborg Healthcare & Medical
In an effort to design smaller, more intricate and complicated medical devices without running afoul of increasingly stringent national and international regulations, many designers are looking to geometric transition extrusions manufactured of high consistency rubber (HCR) silicone. This process reduces total cost of ownership for the original equipment manufacturer while improving part quality and greatly enhancing the types of devices being sought by healthcare medproviders.
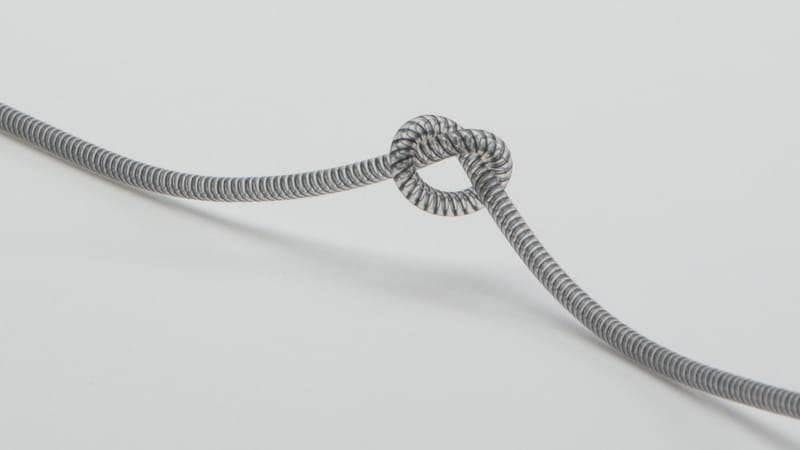
5 medical tubing manufacturing processes to achieve complex geometries
By Dan Sanchez, Trelleborg Healthcare & Medical
Medtech companies have demanded increasingly complex geometries in medical tubing. Here’s a rundown of five manufacturing processes that could help them get there.
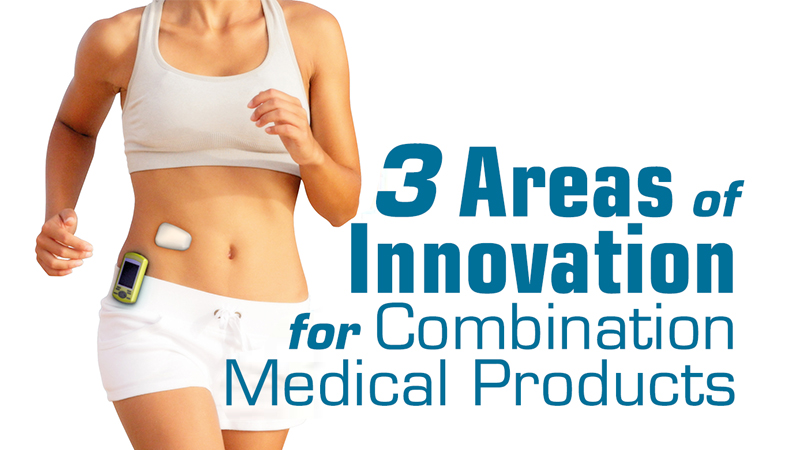
3 Areas of Innovation for Combination Medical Products
By Andrew Gaillard, Global Director and Jonathan Russell, Engineering Manager, Trelleborg Sealing Solutions Healthcare & Medical, published in "Medical Design Briefs" September 2019
Trelleborg is a full-service supplier of finished medical devices involving silicone-API processing, assembly of sensor and insertion device, ready-to-use package and sterilization.
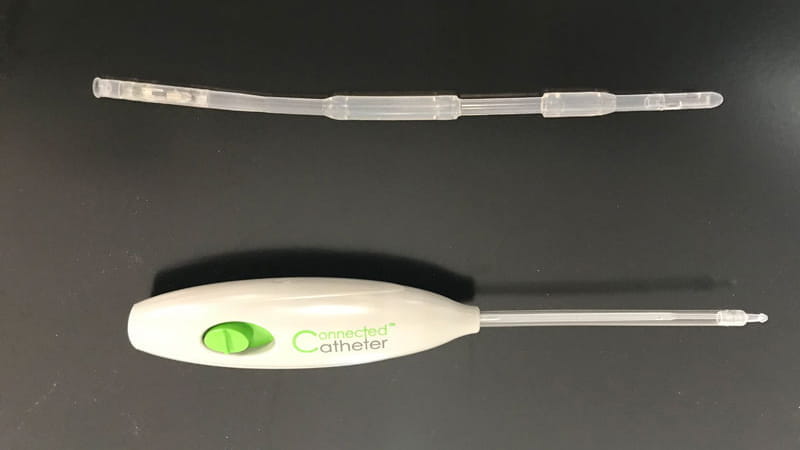
Smart catheter system: A new bladder control management solution
By Michelle Jacobson, published in Today's Medical Developments Magazine, July 2019
With component sourcing and supply chain management support from Trelleborg, Spinal Singularity developed the Connected Catheter to offer improved quality for users.
This article was first published in Today's Medical Developments.
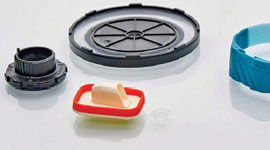
Trelleborg's 2K technology enhances options for medical device manufacturers
By Ursula Nollenberger, published in "Rubber & Plastics News", May 2019
When it comes to the safety and efficiency of medical devices, lives could literally be on the line.
Whether it's a wearable pump for insulin or implantable delivery devices, proper dose regulation and biocompatibility are crucial.
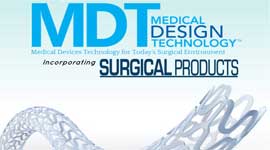
The Power of Combination Medical Products
By Mark Gordon and Andrew Gaillard; published in "MDT-Medical Design Technology", March 2019
As the medical device and pharmaceutical worlds continue to converge, extraordinary product designs are becoming reality
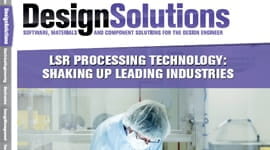
LSR Processing Technology: Shaking up leading industries
Published in "DesignSolutions"
The technical possibilities with liquid silicone rubber (LSR) are endless and can be applied to numerous fields. This article demonstrates how LSR and two-component (or two-shot) injection molding technology can be used across a range of industries to produce innovative solutions.
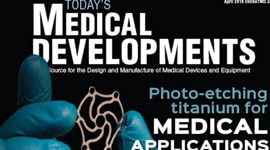
Simple O-ring rises to new levels
By Ursula Nollenberger and Jarno Burkhardt published in "TODAY'S MEDICAL DEVELOPMENTS"
O-Rings are the most popular seals used by design engineers due to their basic geometry and almost universal use. Read this article to learn more about how liquid silicone rubber (LSR) O-Rings are used for healthcare and medical applications.
This article was first published in Today's Medical Developments.
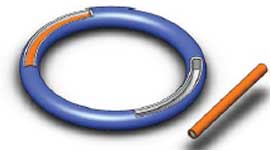
How you can keep Bacteria from colonizing Silicone
Published in "MDO"
Three production techniques can reduce the colonization of bacteria on devices made of silicone for placement inside the body. Tests have shown that the newest method shows promise.
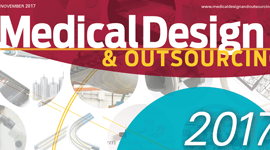
How to make kink-resistant tubing work in smaller medical devices
Published in "Medical Design"
Today's implantable medical devices require bio-friendly silicone that keeps fluids flowing even when space is tight..
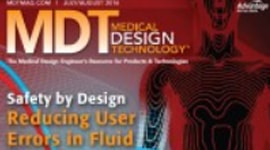
Microneedle Patches - Design for Superior Drug Delivery
Published in Medical Design Technology
Transdermal drug delivery systems have several benefits over traditional methods. Read this article for more information on how liquid silicone rubber can be successfully transformed into microneedle patches designed for this particular use.

Transdermal Drug Delivery & Microneedle Technology
Medical patches have been around for a long time, but new versions with tiny needles could revolutionize drug-delivery. This article takes an in-depth look at the challenges and opportunities microneedle technology offers.

FFKM Sealing Solutions for Pharma & Biotech OEMs
Isolast® FFKMs combine the resilience and sealing force of an elastomer with the chemical inertness and thermal stability of PTFE. ISO 14644-1 certified cleanliness of components throughout the supply chain makes them ideal for use in pharmaceutical and biotechnology equipment, such as mass spectrometers.
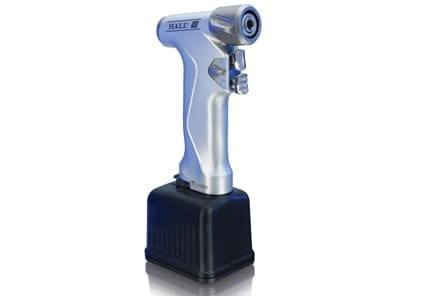
9 Expectations to have of your Suppliers
What our customers should expect from companies within their supply chain.
Medical Design Technology, September 2014