Trelleborg Showcases Healthcare and Medical Innovations and Expertise at Medical Technology UK 2024
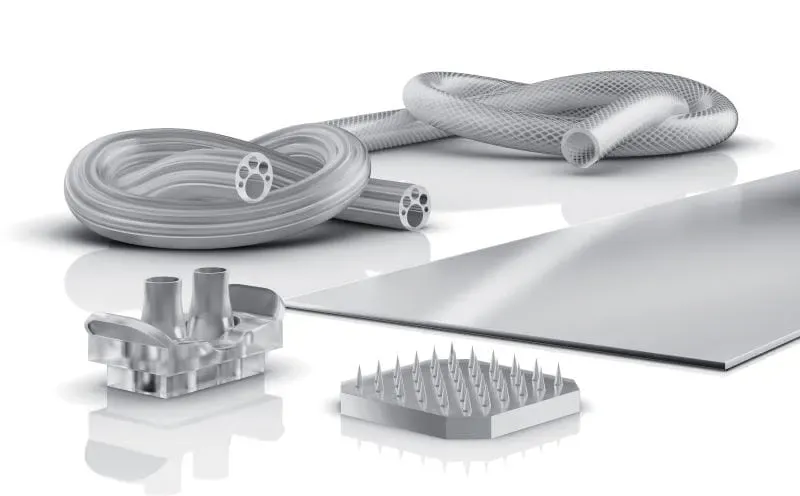
Innovative solutions accelerate the advancement of life-changing therapies
Visitors can learn about Trelleborg’s new BioPharmaPro™ family of innovative products, materials and services for fluid path single-use equipment to accelerate the advancement of life-changing therapies. The BioPharmaPro™ range delivers solutions created from a vast portfolio of materials, including silicones, other elastomers, thermoplastics, and composites, which can be manufactured into tubing, custom molded components, processing columns, up to full assemblies, and much more.
Solutions range from individual single-use components to complex assemblies and full biopharmaceutical systems manufactured from a wide portfolio of polymer materials meeting functionality, cleaning and sterilization, and regulatory requirements. State-of-the-art equipment, processes and advanced manufacturing technology produce innovative and reliable precision components and assemblies created using extrusion, molding, composites and various other technologies.
>>Watch the BioPharmaPro™ webinar
Collaborative development for optimal solutions
Florance Veronelli, Segment Manager Healthcare & Medical Europe, says: ”We build strong partnerships with our customers to collaboratively develop innovative solutions to optimize the outcomes of single-use systems performing critical functions. When customers approach us with their ideas for innovative components and devices, we work with them at every step to turn these ideas into reality.
”BioPharmaPro™’s combination of polymer materials expertise, advanced manufacturing processes, innovative engineering and quality assurance enables us to provide unsurpassed support to accelerate the business of our biopharmaceutical customers.”
>>Find out more about BioPharmaPro™
Novel multicomponent solutions
Trelleborg is also showcasing its multicomponent technology, which pushes the limits of manufacturing innovation to create unique components that no other methods can achieve. Medical equipment manufacturers benefit from a process that helps meet their design goals, including reducing the size and weight of components, while increasing their robustness and improving quality, lowering total cost of ownership.
Trelleborg’s Liquid Silicone Rubber (LSR) experts employ highly sophisticated tools and process engineering to develop novel solutions, combining two, three or more individual materials and components into one fully bonded, robust component. This multi-component injection molding or co-injection – commonly referred to as 2K or 2-shot – produces parts that are more hygienic, eradicating the dead space where bacteria can breed, and lowers costs by cutting out assembly and reducing the number of components in the customer’s supply chain.
>>Find out more about multicomponent technology
A related technology – micromolding - is critical to the miniaturization of devices so small they are wearable and implantable. Components below 10 milligrams in weight are possible using needlepoint injection technology and fully automated parts handling. Trelleborg’s high-dimensional flashless and wasteless design principles create micromolded parts virtually flash-free and not requiring secondary deflashing.
Tony Fagg, Key Account Manager at Trelleborg Sealing Solutions, says: “With the development of ever smaller sophisticated medical devices, component manufacturers are challenged to produce multi-function devices of increasingly compact dimensions. Micromolding and multicomponent LSR technologies provide a solution to this issue.
“Multicomponent molding can extend design options further than any other technology, enabling device developers the opportunity to go beyond simple function. Virtually boundless product profiles and geometries offer medical device designers options that they may not even be aware of.”
Precision molding
Trelleborg Healthcare & Medical is a leading exponent of moldings used in implantable healthcare and medical devices. Utilizing in-house precision tooling and expertise, Trelleborg creates custom silicone and thermoplastic molded parts with tight tolerances, while satisfying the need for rapid product development with quick turnaround prototypes.
Trelleborg will also display specialty extruded tubing and hose materials including silicone tubing with unique biocompatibility and physical durability.
>>Find out more about medical-grade tubing and hose
Drug-eluting silicone solutions
Also featured are Trelleborg’s drug delivery technologies including drug-eluting silicone with active pharmaceutical ingredients (API), and the Seal-Glide® nanoscale surface treatment. This innovative process improves on the friction performance of conventional solutions yet creates a finish up to 50 times thinner.