Facelifted cars
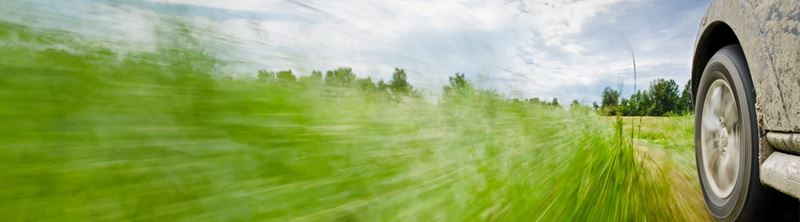
In the Czech Republic, Trelleborg’s sealing profiles operation and its partner Magna are working for a brighter future with lighter cars by supplying a new lightweight bonnet seal – but Trelleborg’s contribution goes far beyond extrusion.
The new bonnet seal is incorporated in Magna’s bumper units, which are fitted on 100,000 vehicles produced in the Czech Republic each year in a joint venture between Toyota, Peugeot and Citroen.
It is the latest in a series of sealing profile projects with Magna, a global automotive parts manufacturer, and one of Europe’s leading tier one suppliers. Trelleborg and Magna have been partners in the Czech Republic for over 10 years, working on a range of sealing solutions for bumpers, rubber sleeves, dashboard gaskets and mud guards for vehicle makers such as Skoda, VW, Audi, Citroen and Toyota.
However, the bonnet seal project represents not only a better, weight-saving solution, but also a new departure for Trelleborg.
New weight-saving bonnet seal design
“The lightweight bonnet seal produced by Trelleborg in partnership with Magna is a new design,” says Otakar Vašák, Country Manager for sealing profiles in the Czech Republic & Slovakia. “Historically, bonnet seals often had a metal insert that clipped onto a metal edge on the bodywork. This new seal design dispenses with metal in favor of plastic pins, which slot into pre-drilled holes in the bodywork. As there is no edge, the bodywork is flat and easier to manufacture, but the biggest benefit is that the seal weighs half as much. It’s also easier to recycle. The customer benefits from the solution as it helps to reduce overall car weight, fuel consumption and CO2 emissions.”
The bonnet seal was predesigned by the car maker, but was adjusted in cooperation with Magna in order for Trelleborg to carry out the additional automated processing stage of inserting the plastic pins into the seal.
“This is something new for Trelleborg as we have implemented a customized machine specifically for this project to carry out the automated pin insertion,” continues Vašák.
The bonnet seal is extruded, vulcanized and pre-cut to length in Värnamo, Sweden. It is then shipped to Trelleborg’s sealing profiles facility in Skózow, Poland, where the customized machine drills holes, automatically inserts the plastic pins in a camera-controlled process and angle-cuts the ends of the gasket to the final length and shape. The bonnet seal is delivered to Magna for final assembly in the bumper unit and then on to the OEM customer in the Czech Republic.
Beyond core business
“Our core business at Trelleborg’s sealing profiles operation is extruded sealing products, but now we are adding automatic operations and new features to produce a final product with added value that the customer can assemble into larger systems,” says Vašák.
“This shows that we are not just a volume supplier of gaskets, but are capable of building in other automatic operations, and we have the higher-level ISO/TS 16949 certification that is required for automotive suppliers.”
“Based on this experience we can create custom-built machines in cooperation with our external machine suppliers to add automatic operations for specific projects. It offers exciting new possibilities for the future,” finishes Vašák.